Vein-proof additive for casting and preparing method thereof
An additive and veining technology is applied in the field of casting additives to achieve the effect of strengthening the chilling effect, improving the thermoplasticity and avoiding the veining defect.
- Summary
- Abstract
- Description
- Claims
- Application Information
AI Technical Summary
Problems solved by technology
Method used
Examples
Embodiment 1
[0029] The anti-veining additive for casting is prepared according to the following method:
[0030] (1) Sieve zircon sand and shale particles with 30-mesh and 100-mesh sieves respectively, and keep the sieve residue between 30-mesh and 100-mesh for later use;
[0031] (2) Sieve the spodumene particles and the ilmenite particles with 50 mesh and 150 mesh sieves respectively, and keep the sieve residue between 50 mesh and 150 mesh sieves for subsequent use;
[0032] (3) Sieve the iron oxide black powder with 100 mesh and 325 mesh sieves, and keep the sieve residue between 100 mesh and 325 mesh sieves for subsequent use;
[0033] (4) Weigh 5% of zircon sand, 25% of shale particles, 40% of spodumene particles, 15% of ilmenite particles, and 15% of iron oxide black powder after sieving, and add them to special mixing equipment in turn , turn on the stirring for mixing, mix evenly and discharge the material for packaging.
Embodiment 2
[0035] The anti-veining additive for casting is prepared according to the following method:
[0036] (1) Sieve the chromite sand and pyrophyllite particles with 30 mesh and 100 mesh sieves respectively, and keep the sieve residue between 30 mesh and 100 mesh for subsequent use;
[0037] (2) Sieve the lithium-phosphorite particles and the rutile particles with 50 mesh and 150 mesh sieves respectively, and keep the sieve residue between 50 mesh and 150 mesh sieves for subsequent use;
[0038] (3) Sieve the iron oxide red powder with 100 mesh and 325 mesh sieves, and keep the sieve residue between 100 mesh and 325 mesh sieves for subsequent use;
[0039] (4) Weigh 12% of chromite sand, 19% of pyrophyllite particles, 30% of spodumene particles, 19% of ilmenite particles, and 20% of red iron oxide powder after sieving, and add them to special mixing equipment in turn , turn on the stirring for mixing, mix evenly and discharge the material for packaging.
Embodiment 3
[0041] The anti-veining additive for casting is prepared according to the following method:
[0042] (1) Sieve the olivine sand and mica particles with 30 mesh and 100 mesh sieves respectively, and keep the sieve residue between 30 mesh and 100 mesh for subsequent use;
[0043] (2) Sieve the lithium petalite particles and ilmenite particles with 50 mesh and 150 mesh sieves respectively, and keep the sieve residue between 50 mesh and 150 mesh sieves for subsequent use;
[0044] (3) Sieve the oxidized black-red powder with 100 mesh and 325 mesh sieves, and keep the sieve residue between 100 mesh and 325 mesh sieves for subsequent use;
[0045] (4) Weigh 10% of olivine sand, 16% of mica, 55% of petalite feldspar, 11% of ilmenite particles, and 8% of iron oxide black powder after sieving, and add them to special mixing equipment in turn, and start Stir for mixing, mix evenly, and then discharge and pack.
PUM
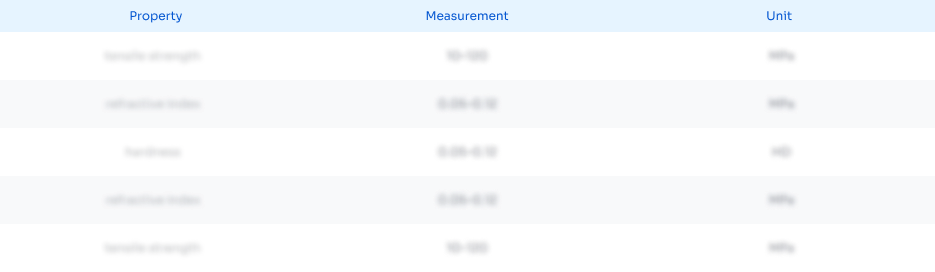
Abstract
Description
Claims
Application Information

- R&D
- Intellectual Property
- Life Sciences
- Materials
- Tech Scout
- Unparalleled Data Quality
- Higher Quality Content
- 60% Fewer Hallucinations
Browse by: Latest US Patents, China's latest patents, Technical Efficacy Thesaurus, Application Domain, Technology Topic, Popular Technical Reports.
© 2025 PatSnap. All rights reserved.Legal|Privacy policy|Modern Slavery Act Transparency Statement|Sitemap|About US| Contact US: help@patsnap.com