Secondary zinc oxide recycling method
A technology of secondary zinc oxide and leaching solution, applied in the field of metallurgy and chemical industry, can solve the problems of aggravation, anode damage, affecting the electrolysis process, etc., and achieve the effect of low cost and good effect.
- Summary
- Abstract
- Description
- Claims
- Application Information
AI Technical Summary
Problems solved by technology
Method used
Examples
Embodiment 1
[0021] A kind of secondary zinc oxide reutilization method, it is to take the electric furnace dedusting ash of iron and steel plant as main raw material, then reclaim through following steps:
[0022] a. Mix the dust from iron and steel plant with bituminous coal and send it to the rotary kiln for roasting;
[0023] b. Carrying out alkaline washing and leaching of the roasted cooling product in step a with soda solution, and separating to obtain the leaching solution;
[0024] c. Add hydrogen peroxide to the leaching solution and filter out the precipitated substance;
[0025] d, adding zinc and copper sulfate to the leaching solution and filtering out the precipitated substance;
[0026] e, the leachate is subjected to ion exchange treatment;
[0027] f. Electrolyzing the solution obtained after ion exchange to precipitate zinc.
[0028] The iron and steel factory dust and bituminous coal are mixed at a ratio of 1:1, and the mixture is conveyed into the rotary kiln by a s...
Embodiment 2
[0030] A kind of secondary zinc oxide reutilization method, it is to take the electric furnace dedusting ash of iron and steel plant as main raw material, then reclaim through following steps:
[0031] a. Mix the dust from iron and steel plant with bituminous coal and send it to the rotary kiln for roasting;
[0032] b. Carrying out alkaline washing and leaching of the roasted cooling product in step a with soda solution, and separating to obtain the leaching solution;
[0033] c. Add hydrogen peroxide to the leaching solution and filter out the precipitated substance;
[0034] d, adding zinc and copper sulfate to the leaching solution and filtering out the precipitated substance;
[0035] e, the leachate is subjected to ion exchange treatment;
[0036] f. Electrolyzing the solution obtained after ion exchange to precipitate zinc.
[0037] The iron and steel factory dust and bituminous coal are mixed at a ratio of 3:1, and the mixture is conveyed into a rotary kiln by a scr...
Embodiment 3
[0039] A kind of secondary zinc oxide reutilization method, it is to take the electric furnace dedusting ash of iron and steel plant as main raw material, then reclaim through following steps:
[0040] a. Mix the dust from iron and steel plant with bituminous coal and send it to the rotary kiln for roasting;
[0041] b. Carrying out alkaline washing and leaching of the roasted cooling product in step a with soda solution, and separating to obtain the leaching solution;
[0042] c. Add hydrogen peroxide to the leaching solution and filter out the precipitated substance;
[0043] d, adding zinc and copper sulfate to the leaching solution and filtering out the precipitated substance;
[0044] e, the leachate is subjected to ion exchange treatment;
[0045] f. Electrolyzing the solution obtained after ion exchange to precipitate zinc.
[0046] The iron and steel plant dust and bituminous coal are mixed at a ratio of 6:1, and the mixture is conveyed into a rotary kiln by a screw...
PUM
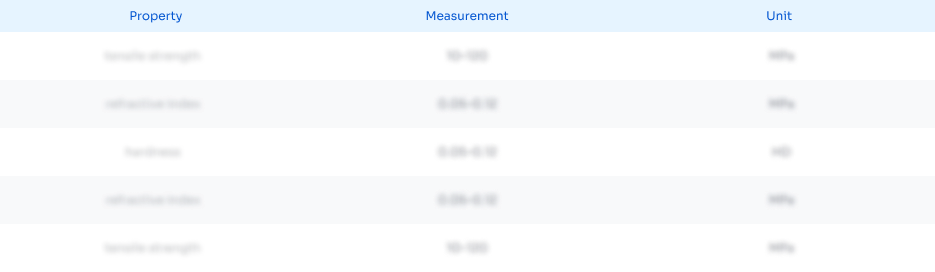
Abstract
Description
Claims
Application Information

- R&D
- Intellectual Property
- Life Sciences
- Materials
- Tech Scout
- Unparalleled Data Quality
- Higher Quality Content
- 60% Fewer Hallucinations
Browse by: Latest US Patents, China's latest patents, Technical Efficacy Thesaurus, Application Domain, Technology Topic, Popular Technical Reports.
© 2025 PatSnap. All rights reserved.Legal|Privacy policy|Modern Slavery Act Transparency Statement|Sitemap|About US| Contact US: help@patsnap.com