Process for cleaning accelerator NS produced by oxygen oxidation method of crude product M
A technology of oxygen oxidation and accelerator, which is applied in the field of rubber accelerators, can solve the problems of failure to meet quality requirements, low yield of accelerator NS, large amount of tert-butylamine, etc., to improve product color, low production cost, and product quality high effect
- Summary
- Abstract
- Description
- Claims
- Application Information
AI Technical Summary
Problems solved by technology
Method used
Image
Examples
Embodiment 1
[0047] Add aniline, carbon disulfide, and sulfur into a closed container at a ratio of 1:1.2:1, and conduct a condensation reaction at 265°C under a controlled pressure of 11MPa for 8 hours to obtain a crude accelerator M with a content of 93%; mix the crude accelerator M with 10% mass The concentrated ammonia water was stirred at 45°C with a ratio of 1:4 (mass ratio), and air was blown in. After the upper layer RS- became a transparent liquid, the stirring was stopped and the interface phenomenon appeared (the time for blowing air was 0.5 hours), liquid separation, the lower layer of precipitation as solid waste treatment, get the supernatant for use;
[0048] After inserting the solid catalyst, stir the supernatant and tert-butylamine evenly at a ratio of 1:3.6 (molar ratio); after sealing the container, introduce oxygen, control the oxygen pressure to maintain at 0.4MPa, and stop the reaction after the oxygen is no longer consumed. After centrifugal separation, washing and ...
Embodiment 2
[0052] Stir the residual crude product M with a content of 77% (the impurity is tar resin) and 20% mass concentration of ammonia water at a ratio of 1:5.5 (mass ratio) at 55°C, blow in air, and wait until the upper RS- When it is a transparent liquid, stop stirring and precipitate and appear interface phenomenon (the time of air bubbling is 1 hour), separate the liquid, and the lower layer of sediment is treated as solid waste, and the supernatant is taken for use;
[0053] After inserting the solid catalyst, stir the supernatant and tert-butylamine at a ratio of 1:2.7 (molar ratio); after sealing the container, introduce oxygen, control the oxygen pressure to maintain at 0.35MPa, and stop the reaction after the oxygen is not consumed. After centrifugal separation, washing and drying, the product is obtained. The product yield is 96.5%, the initial melting point is 105.8° C., and the product purity is 97%. The product quality has reached the national standard.
[0054] Where...
Embodiment 3
[0057] Stir the residual crude product M with a content of 77% (the impurity is tar resin), 30% mass concentration of ammonia water at a ratio of 1:5.5 (mass ratio) at 50°C, blow in air, and wait for the upper layer RS - After turning into a transparent liquid, stop stirring and settling, and interface phenomena will appear (the time for air bubbling is 0.8 hours), separate the liquid, and the lower layer of precipitation will be treated as solid waste, and the supernatant liquid will be taken for use;
[0058] After inserting the solid catalyst, stir the supernatant and tert-butylamine at a ratio of 1:3 (molar ratio); after sealing the container, introduce oxygen and keep the pressure at 0.2MPa, and the reaction will be terminated after the oxygen is no longer consumed. After centrifugal separation, washing and drying, the product is obtained. It is known that the product yield is 96.9%, the initial melting point is 106.2°C, and the product purity is 98.6% through assay. The...
PUM
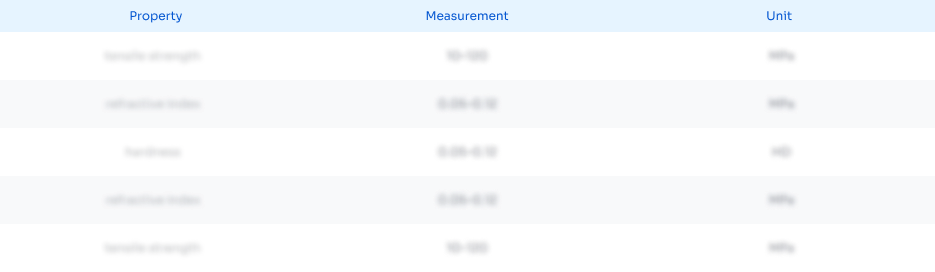
Abstract
Description
Claims
Application Information

- R&D Engineer
- R&D Manager
- IP Professional
- Industry Leading Data Capabilities
- Powerful AI technology
- Patent DNA Extraction
Browse by: Latest US Patents, China's latest patents, Technical Efficacy Thesaurus, Application Domain, Technology Topic, Popular Technical Reports.
© 2024 PatSnap. All rights reserved.Legal|Privacy policy|Modern Slavery Act Transparency Statement|Sitemap|About US| Contact US: help@patsnap.com