Bionic anti-sticking surface and preparation method thereof
An anti-adhesive and rough blank technology, which is applied in the field of bionic anti-adhesive surface and its preparation, can solve the problems that cannot effectively solve the problem of high-viscosity resin adhesion, affect the prepreg molding process, increase the difficulty and cost of cleaning, and achieve excellent results. Anti-resin adhesion ability, uniform structure size and spacing, and effect of reducing surface energy
- Summary
- Abstract
- Description
- Claims
- Application Information
AI Technical Summary
Problems solved by technology
Method used
Image
Examples
Embodiment 1
[0036] A bionic anti-sticking surface, the specific steps of its preparation process are as follows:
[0037] Step 1. Select tungsten high-speed steel W18Cr4V, cut the steel into 40×40mm square samples, and then polish the samples with 300#, 500#, 800#, 1200#, 2000# sandpaper in order to remove the oxide layer on the surface of the steel and ensure The surface has a certain flatness, and a rough billet is obtained;
[0038] Step 2: Ultrasonic cleaning the rough billet 1 with deionized water, acetone and absolute ethanol in sequence to remove impurities and oil stains on the steel surface, and vacuum drying to obtain rough billet 2;
[0039] Step 3 Use nanosecond laser to process "mastoid" structures with different diameters, the diameters are 100 μm, 200 μm, 300 μm, 400 μm, 500 μm, the spacing is 100 μm, and the laser scanning rate is 200 mm / s to obtain rough blank 3.
[0040] Step 4: Immerse rough billet 3 in an acidic rust remover for 5 minutes, and scrub the processed surf...
Embodiment 2
[0044] The difference from Example 1 is that in Step 3, the diameter of the laser-processed "mastoid" structure is 100 μm, the pitches are 100 μm, 200 μm, 300 μm, 400 μm, and 500 μm, and the scanning rate is 200 mm / s.
[0045] In this example, the contact angle and rolling angle tests of water and resin were carried out on the final sample, and the water and resin droplet volume was 4 μl. The test results show that the "papillary" diameter is 100 μm, the spacing is 100 μm, and the laser scanning rate is 200 mm / s. The contact angle and rolling angle are 147.5° and 9.4°, respectively. Therefore, the "mastoid" prepared in this example has a diameter of 100 μm, a spacing of 100 μm, and a laser scanning rate of 200 mm / s on the surface of the sample, which has a better anti-resin adhesion effect.
Embodiment 3
[0047] The difference from the above example 1 is that in step 3, the diameter of the laser-processed "mastoid" structure is 100 μm, the spacing is 100 μm, and the scanning speed is 800mm / s, 400mm / s, 300mm / s, 200mm / s, 100mm / s.
[0048] In this example, the contact angle and rolling angle tests of water and resin were carried out on the final sample, and the water and resin droplet volume was 4 μl. The test results show that the "papillary" diameter is 100 μm, the spacing is 100 μm, and the laser scanning rate is 100 mm / s. The contact angle and rolling angle are 149.7° and 7.3°, respectively. Therefore, the surface of the biomimetic protrusion structural steel prepared in this example has a better anti-resin adhesion effect. And compared with the optimal sample surface in Examples 1 and 2, the test effect of this sample is better. figure 2 is the SEM image of the surface of the sample with the "mastoid" having a diameter of 100 μm, a pitch of 100 μm, and a laser scanning r...
PUM
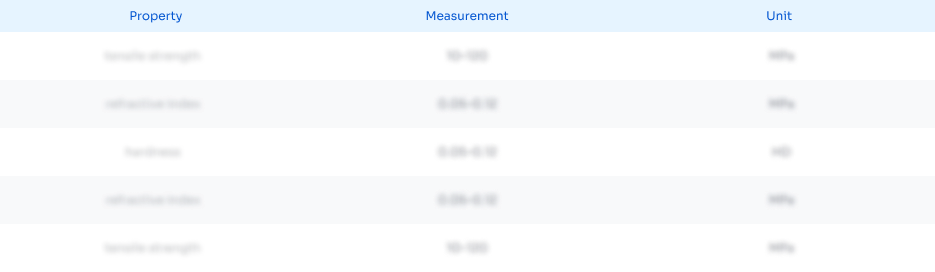
Abstract
Description
Claims
Application Information

- R&D Engineer
- R&D Manager
- IP Professional
- Industry Leading Data Capabilities
- Powerful AI technology
- Patent DNA Extraction
Browse by: Latest US Patents, China's latest patents, Technical Efficacy Thesaurus, Application Domain, Technology Topic, Popular Technical Reports.
© 2024 PatSnap. All rights reserved.Legal|Privacy policy|Modern Slavery Act Transparency Statement|Sitemap|About US| Contact US: help@patsnap.com