Novel composite putty for surface repairing of steel structure components
A steel structure, surface repair technology, applied in the direction of filling slurry, etc., can solve the problems of matrix metal structure corrosion failure, easy to form cracks, no electrochemical protection performance, etc., to achieve the effect of improving anti-corrosion performance
- Summary
- Abstract
- Description
- Claims
- Application Information
AI Technical Summary
Problems solved by technology
Method used
Image
Examples
Embodiment 1
[0018] A new type of composite putty for repairing the surface of a steel structure is composed of a main body ash and a curing agent, and the mass ratio of the main body ash and the curing agent is 100:2 when used. The main body ash is composed of the following components by weight: 50 parts of water-based carbon-titanium cage resin, 10 parts of deionized water, 1 part of BYK-980, 0.1 part of ethylparaben, 0.02 part of polyamide wax, polymethacrylic acid 0.5 part of methyl ester, 0.3 part of dimethylaniline, 0.08 part of methyl ethyl ketoxime, 3 parts of talc, 4 parts of barium sulfate, 8 parts of titanium dioxide, 7 parts of metal Zn powder, and 16 parts of copper-plated nylon fibers. The curing agent is composed of the following components by weight: 60 parts of benzoyl peroxide, 30 parts of dibutyl phthalate, and 10 parts of silicon dioxide.
[0019] The preparation of the main ash includes: respectively adding water-based carbon-titanium cage resin, deionized water, BYK-9...
Embodiment 2
[0028] A new type of composite putty for repairing the surface of a steel structure is composed of a main body ash and a curing agent, and the mass ratio of the main body ash and the curing agent is 100:2 when used. The main ash is composed of the following components by weight: 60 parts of water-based carbon-titanium cage resin, 4 parts of deionized water, 3 parts of BYK-980, 0.02 parts of ethyl paraben, 0.03 parts of polyamide wax, polymethacrylic acid 0.8 part of methyl ester, 0.1 part of dimethylaniline, 0.05 part of methyl ethyl ketoxime, 1 part of talc, 3 parts of barium sulfate, 7 parts of titanium dioxide, 10 parts of metal Zn powder, and 11 parts of galvanized polyimide fiber. The curing agent is composed of the following components by weight: 64 parts of benzoyl peroxide, 24 parts of dibutyl phthalate, and 12 parts of silicon dioxide.
[0029] The preparation of the main body ash includes respectively adding water-based carbon-titanium cage resin, deionized water, BY...
PUM
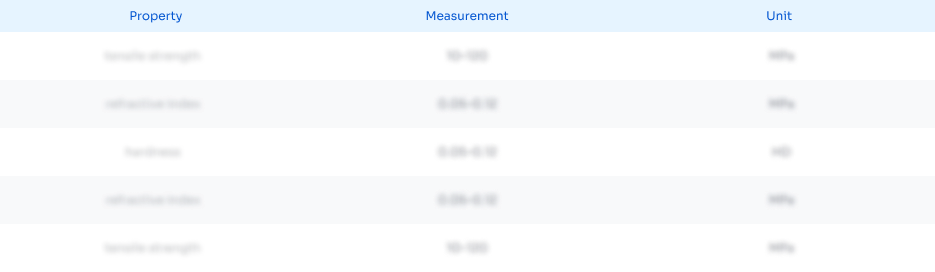
Abstract
Description
Claims
Application Information

- Generate Ideas
- Intellectual Property
- Life Sciences
- Materials
- Tech Scout
- Unparalleled Data Quality
- Higher Quality Content
- 60% Fewer Hallucinations
Browse by: Latest US Patents, China's latest patents, Technical Efficacy Thesaurus, Application Domain, Technology Topic, Popular Technical Reports.
© 2025 PatSnap. All rights reserved.Legal|Privacy policy|Modern Slavery Act Transparency Statement|Sitemap|About US| Contact US: help@patsnap.com