Dry-spot-preventing additive, preparation method and application thereof to waterborne cathodic electrophoretic paint
An additive and dry spot technology, applied in electrophoretic coatings, coatings, etc., can solve problems such as easy dry spots, and achieve the effects of preventing dry spot defects, facilitating popularization and application, and smooth appearance
- Summary
- Abstract
- Description
- Claims
- Application Information
AI Technical Summary
Problems solved by technology
Method used
Image
Examples
preparation example Construction
[0070] Preparation of F2 electrophoretic color paste: After the dispersing resin is dispersed in water at high speed, add pigments and fillers to disperse at high speed for 30 minutes, transfer to a sand mill at 1800 rpm, and grind for 2 hours until the fineness is ≤10 μm.
[0071] The method of use of this coating is:
[0072] Mix the F1 and F2 of the coating and pour it into the electrophoresis tank of 2000mm×500mm×1500mm, and put it in
[0073] 1500mm×6mm×1000mm surface-treated steel plate, connected to the cathode, turn on the electrophoretic coating equipment, and complete the electrophoresis experiment according to the conditions of the coating equipment; take out the workpiece, hang it for 15 minutes, then rinse the workpiece with water, and observe after stopping The condition of color spots on the surface of the workpiece; bake the workpiece, take it out and observe the condition of color spots on the surface of the workpiece. The improvement in dry spot additives wa...
Embodiment 1-10
[0076] According to the formula ratio of the electrophoretic coating described in the present invention, the electrophoretic coating is prepared by using dry spot additives with different formulas, and the coating is carried out according to the usage method of the coating under the same construction conditions. The formulation of the dry spot additive is shown in the table below:
[0077] Example
1
2
3
4
5
6
7
8
9
10
AMINE C-12
0
10
0
10
0
0
50
0
15
0
AMINE C-17
20
0
10
10
30
40
0
0
0
15
FS-82
2.5
2.5
0
0
0
6
10
0
20
0
FS-202
0
0
2.5
3
5
0
0
30
0
30
FS-204
10
0
10
0
0
0
0
0
0
0
FS-304
0
10
0
10
30
0
0
0
0
0
FS-640
10
0
20
0
0
10
0
0
15
5
FS-680
0
50
0
0
20
0
...
PUM
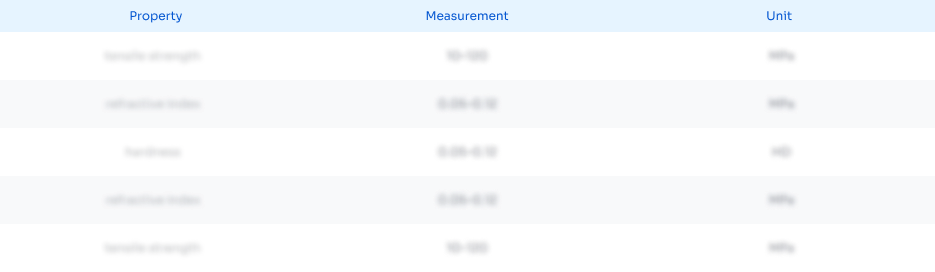
Abstract
Description
Claims
Application Information

- Generate Ideas
- Intellectual Property
- Life Sciences
- Materials
- Tech Scout
- Unparalleled Data Quality
- Higher Quality Content
- 60% Fewer Hallucinations
Browse by: Latest US Patents, China's latest patents, Technical Efficacy Thesaurus, Application Domain, Technology Topic, Popular Technical Reports.
© 2025 PatSnap. All rights reserved.Legal|Privacy policy|Modern Slavery Act Transparency Statement|Sitemap|About US| Contact US: help@patsnap.com