Refining method of industrial sodium chloride waste salt residues
A refining method and sodium chloride technology, which is applied in the purification of alkali metal chlorides and alkali metal halides, can solve the problems that the treatment process does not consider the purification of salt solution, increases the complexity of the treatment process, and is difficult to ensure the quality of product salt. , to achieve good heat treatment effect, good energy saving effect, and small secondary pollution
- Summary
- Abstract
- Description
- Claims
- Application Information
AI Technical Summary
Problems solved by technology
Method used
Image
Examples
Embodiment 1
[0045] The waste salt slag to be treated in this embodiment is pale yellow, containing 87.26% (wt%) of sodium chloride salt, 3.04% (wt%) of organic matter, 5.31% (wt%) of moisture, 0.45% (wt%) of metal impurities such as calcium and magnesium %), sulfate radical 3.6% (wt%), water-insoluble matter 0.32% (wt%), above-mentioned sodium chloride waste salt slag is after 300 ℃ of heat treatment 180min, dissolves with 60 ℃ of hot water, and the chlorine that obtains after filtering and purifying evaporates Sodium chloride content is 99.40% (wt%) in the sodium chloride product, and moisture is 0.31% (wt%), and water-insoluble matter is 0.06% (wt%), and the total amount of calcium and magnesium is 0.11% (wt%), and sulfate radical The content is 0.07% (wt%), reaching the first grade standard of refined industrial salt and industrial dry salt.
Embodiment 2
[0047] The waste salt to be treated in this embodiment is yellow-brown, containing 78.83% (wt%) of sodium chloride salt, 9.92% (wt%) of organic matter, 7.7% (wt%) of moisture, 0.33% (wt%) of metal impurities such as calcium and magnesium ), phosphate root 2.6% (wt%), water insoluble matter 0.59% (wt%), above-mentioned sodium chloride waste salt slag is after 550 ℃ of heat treatment 40min, dissolves with 80 ℃ of hot water, and the chlorination that obtains after filtering and purifying evaporation In the sodium product, the sodium chloride content is 99.35% (wt%), the moisture is 0.46% (wt%), the water insoluble matter is 0.06% (wt%), the total amount of calcium and magnesium is 0.08% (wt%), and the phosphate content It is 0.01% (wt%), reaching the first-class standard of industrial dry salt (industrial salt "GB / T5462-2015").
Embodiment 3
[0049] The waste salt slag to be treated in this embodiment is light brown, containing 71.33% (wt%) of sodium chloride salt, 9.73% (wt%) of organic matter, 10.5% (wt%) of moisture, 0.36% (wt%) of metal impurities such as calcium and magnesium %), sulfate radical 7.6% (wt%), water insoluble matter 0.41% (wt%), after above-mentioned sodium chloride waste salt slag 700 ℃ of heat treatment 20min, dissolve with 40 ℃ of hot water, filter and purify the chlorination that obtains after evaporation In the sodium product, the sodium chloride content is 99.41% (wt%), the moisture is 0.35% (wt%), the water insoluble matter is 0.05% (wt%), the total amount of calcium and magnesium is 0.07% (wt%), the sulfate content It is 0.06% (wt%), reaching the first-class standard of industrial dry salt (industrial salt "GB / T5462-2015").
[0050] The comparison between the method of this aspect and other processing schemes to process the product components is shown in Table 1.
[0051] Table 1 This me...
PUM
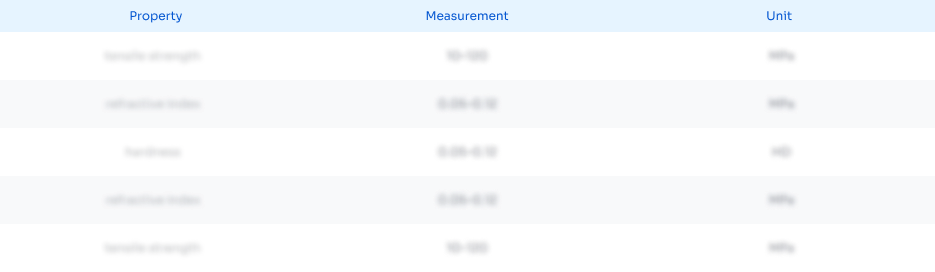
Abstract
Description
Claims
Application Information

- R&D Engineer
- R&D Manager
- IP Professional
- Industry Leading Data Capabilities
- Powerful AI technology
- Patent DNA Extraction
Browse by: Latest US Patents, China's latest patents, Technical Efficacy Thesaurus, Application Domain, Technology Topic, Popular Technical Reports.
© 2024 PatSnap. All rights reserved.Legal|Privacy policy|Modern Slavery Act Transparency Statement|Sitemap|About US| Contact US: help@patsnap.com