Automotive interior trim basting stitch process
A technology for automobile interior decoration and stitching, which is applied to household components, household appliances, other household appliances, etc., can solve the problems of slow speed, poor quality and high processing cost, and achieve uniform skin texture, low equipment cost and fast processing speed. Effect
- Summary
- Abstract
- Description
- Claims
- Application Information
AI Technical Summary
Problems solved by technology
Method used
Examples
Embodiment Construction
[0007] First, the flame robot is used to extract the grease of the skeleton. After the degreasing treatment is completed, the surface of the skeleton is sprayed with two-component glue with a glue spraying equipment;
[0008] Install the electroforming mold on the hot press molding machine, put the glue-sprayed interior panel skeleton on the punch of the hot press molding machine, and then put the skin on the heating plate of the hot press molding machine to heat the skin and heat it. The temperature is 190-210°C, and the heated skin is moved to the concave mold. The concave mold is provided with skin patterns and stitch patterns. The upper and lower molds are clamped to vacuum force to preform the heated skin, so that the skin is printed with patterns and patterns. The suture pattern makes the skin conform to the shape; then the skin and the interior panel skeleton are combined into one, after the molding is completed, the removal action is completed, and the excess process ed...
PUM
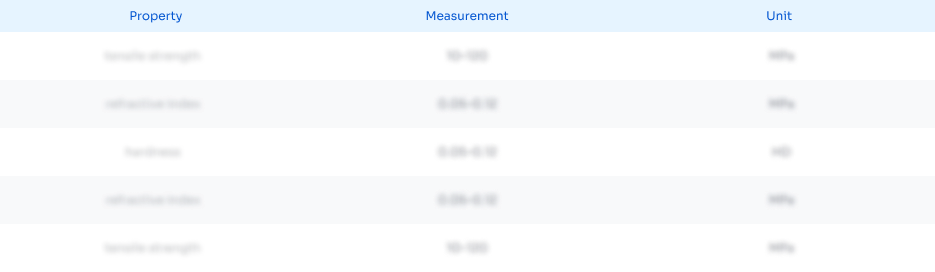
Abstract
Description
Claims
Application Information

- R&D
- Intellectual Property
- Life Sciences
- Materials
- Tech Scout
- Unparalleled Data Quality
- Higher Quality Content
- 60% Fewer Hallucinations
Browse by: Latest US Patents, China's latest patents, Technical Efficacy Thesaurus, Application Domain, Technology Topic, Popular Technical Reports.
© 2025 PatSnap. All rights reserved.Legal|Privacy policy|Modern Slavery Act Transparency Statement|Sitemap|About US| Contact US: help@patsnap.com