Conditioning method for polishing pad, and chemical-mechanical polishing method and device
A chemical machinery and grinding device technology, used in grinding devices, grinding machine tools, abrasive surface adjustment devices, etc., can solve the problems of inaccurate leveling parameters, inability to reach the surface of the grinding pad, affecting the good rate of the CMP process, etc. performance effect
- Summary
- Abstract
- Description
- Claims
- Application Information
AI Technical Summary
Problems solved by technology
Method used
Image
Examples
Embodiment 1
[0054] figure 1 It is a flow chart of the polishing pad dressing method according to Embodiment 1 of the present invention. Such as figure 1 As shown, Embodiment 1 may include the following steps:
[0055] S101. Receive surface roughness data of the polishing pad sent by the roughness detection device within a preset time; wherein, the surface roughness data is obtained by the roughness detection device by measuring the surface of the polishing pad.
[0056] Such as figure 2 As shown, the chemical mechanical polishing apparatus generally includes a polishing table 10 , a polishing pad 20 , a dresser 40 , a distribution tube 50 and a controller 70 . Wherein, in the CMP process, the polishing pad 20 is arranged on the polishing table, the wafer 30 is arranged on the described polishing pad 20 with the direction facing the described polishing pad, the polishing table 10 rotates in one direction, and the polishing table 10 is set There is a rotating mechanism 101, and the end...
Embodiment 2
[0065] in such as figure 1 On the basis of the first embodiment shown, the embodiment of the present invention also provides image 3 The second embodiment shown.
[0066] S301. Receive surface roughness data of the polishing pad sent by the roughness detection device within a preset time; wherein, the surface roughness data is obtained by the roughness detection device by measuring the surface of the polishing pad.
[0067] The specific structure of the chemical mechanical polishing device is as described in Embodiment 1, and will not be repeated here. The preset time in this embodiment usually refers to a preset time interval, that is to say, the surface roughness data of the polishing pad is acquired every certain time interval. This ensures that the surface roughness of the polishing pad is kept in an optimal state throughout the grinding process.
[0068] S302. Perform calculation according to the surface roughness data to obtain leveling parameters for dressing the po...
Embodiment 3
[0079] Such as Figure 5 Shown is a flow chart of the chemical mechanical polishing method in Embodiment 3 of the present invention. The chemical mechanical polishing method that the present invention implements three comprises the steps:
[0080] S501, grind the object to be ground on the grinding pad, and execute step S505.
[0081] Specifically, the objects to be ground include substrates such as semiconductor objects to be ground. During the grinding process, the object to be ground is placed on the grinding pad, and the grinding pad is located on the grinding table. The polishing liquid pumped in by the liquid pump is continuously supplied to the polishing pad, so the chemical mechanical polishing process is to use the chemical additives in the polishing liquid to produce a chemical reaction on the surface of the object to be ground in contact with the polishing pad to form a An easy-to-grind layer, combined with mechanical grinding assisted by abrasive grains in the p...
PUM
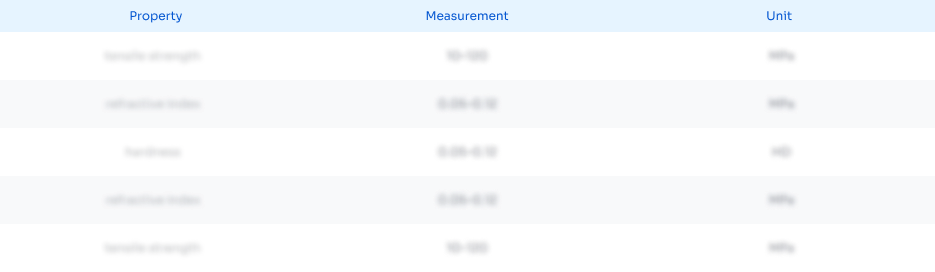
Abstract
Description
Claims
Application Information

- Generate Ideas
- Intellectual Property
- Life Sciences
- Materials
- Tech Scout
- Unparalleled Data Quality
- Higher Quality Content
- 60% Fewer Hallucinations
Browse by: Latest US Patents, China's latest patents, Technical Efficacy Thesaurus, Application Domain, Technology Topic, Popular Technical Reports.
© 2025 PatSnap. All rights reserved.Legal|Privacy policy|Modern Slavery Act Transparency Statement|Sitemap|About US| Contact US: help@patsnap.com