Preparation technology of high-weather-resistance anti-fogging heat insulation membrane
A preparation process and heat insulation film technology, which is applied in the direction of coating, reflection/signal coating, etc., can solve the problems of anti-fog heat insulation film wear resistance, insufficient weather resistance, short anti-fog time, low ultraviolet reflectance, etc., to achieve Weather resistance and stability are not easy, enhance the anti-fog effect, and prolong the effect of anti-fog time
- Summary
- Abstract
- Description
- Claims
- Application Information
AI Technical Summary
Problems solved by technology
Method used
Examples
preparation example Construction
[0032] A preparation process of a highly weather-resistant anti-fog and heat-insulating film, the parts by weight of each component in the formula are:
[0033] Silicon nitride whiskers 20-30 parts,
[0034] Mass fraction 3% sodium dodecylbenzenesulfonate solution 80-120 parts,
[0035] 400-600 parts of mass fraction 80% ethanol solution,
[0036] 20-22 parts of tetraethyl orthosilicate,
[0037] 0.5-0.7 parts of methacryloxypropyltrimethoxysilane,
[0038] 50-60 parts of methacrylic acid,
[0039] Hydrophilic heat curing solvent-based acrylic resin 9-14 parts,
[0040] 55-76 parts of propylene glycol methyl ether,
[0041] 3-10 parts of dimethylformamide,
[0042] 1-5 parts of catalyst triethylenediamine,
[0043] Leveling agent 1-5 parts,
[0044] 5-26 parts of isopropanol,
[0045] 5-24 parts of ethanol;
[0046] Concrete preparation steps are as follows:
[0047] Step 1: Mix silicon nitride whiskers with 3% sodium dodecylbenzenesulfonate solution by mass fractio...
Embodiment 1
[0059] A preparation process of a highly weather-resistant anti-fog and heat-insulating film, the parts by weight of each component in the formula are:
[0060] Silicon nitride whiskers 20 parts,
[0061] Mass fraction 3% sodium dodecylbenzenesulfonate solution 80 parts,
[0062] 400 parts of mass fraction 80% ethanol solution,
[0063] 20 parts of ethyl orthosilicate,
[0064] 0.5 parts of methacryloxypropyltrimethoxysilane,
[0065] 50 parts of methacrylic acid,
[0066] Hydrophilic heat curing solvent-based acrylic resin 9 parts,
[0067] 55 parts of propylene glycol methyl ether,
[0068] 3 parts of dimethylformamide,
[0069] 1 part of catalyst triethylenediamine,
[0070] Leveling agent 1 part,
[0071] 5 parts of isopropanol,
[0072] 5 parts of ethanol;
[0073] Concrete preparation steps are as follows:
[0074] Step 1: Mix silicon nitride whiskers with 3% sodium dodecylbenzenesulfonate solution by mass fraction, stir and mix for 30 minutes to obtain silico...
Embodiment 2
[0085] A preparation process of a highly weather-resistant anti-fog and heat-insulating film, the parts by weight of each component in the formula are:
[0086] Silicon nitride whiskers 30 parts,
[0087] Mass fraction 3% sodium dodecylbenzenesulfonate solution 120 parts,
[0088] 600 parts of mass fraction 80% ethanol solution,
[0089] 22 parts of ethyl orthosilicate,
[0090] 0.7 parts of methacryloxypropyltrimethoxysilane,
[0091] 60 parts of methacrylic acid,
[0092] Hydrophilic heat curing solvent-based acrylic resin 14 parts,
[0093] 76 parts of propylene glycol methyl ether,
[0094] 10 parts of dimethylformamide,
[0095] 5 parts of catalyst triethylenediamine,
[0096] Leveling agent 5 parts,
[0097] 26 parts of isopropanol,
[0098] 24 parts of ethanol;
[0099] Concrete preparation steps are as follows:
[0100] Step 1: Mix silicon nitride whiskers with 3% sodium dodecylbenzenesulfonate solution by mass fraction, stir and mix for 50 minutes to obtain...
PUM
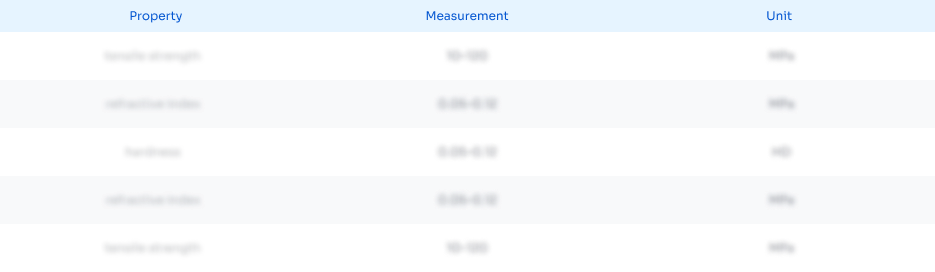
Abstract
Description
Claims
Application Information

- R&D
- Intellectual Property
- Life Sciences
- Materials
- Tech Scout
- Unparalleled Data Quality
- Higher Quality Content
- 60% Fewer Hallucinations
Browse by: Latest US Patents, China's latest patents, Technical Efficacy Thesaurus, Application Domain, Technology Topic, Popular Technical Reports.
© 2025 PatSnap. All rights reserved.Legal|Privacy policy|Modern Slavery Act Transparency Statement|Sitemap|About US| Contact US: help@patsnap.com