On-spot connection joint and method for reinforced thermoplastic plastic pipes
A technology of enhanced thermoplasticity and on-site connection, applied in the direction of pipe/pipe joint/fitting, sleeve/socket connection, through components, etc., which can solve the problems of poor gas tightness of threaded connection, limited connection operation conditions, and insufficient connection reliability, etc. , to achieve the effect of improving connection sealing, improving connection reliability and construction efficiency, and improving corrosion resistance
- Summary
- Abstract
- Description
- Claims
- Application Information
AI Technical Summary
Problems solved by technology
Method used
Image
Examples
Embodiment 1--2
[0025] Example 1--2 RTP pipes 3 connections
[0026] 1) Put two outer sleeves made of 20# steel on the outside of the two RTP pipes 3 respectively;
[0027] 2) Two pairs of sealing grooves are formed at both ends of the 316 material connecting pipe with teeth. Place 4 silicone rubber sealing rings in the sealing grooves at both ends of the 316 material connecting pipe respectively, and then evenly coat the parts with teeth. Apply EVA hot melt adhesive;
[0028] 3) Insert the two ends of the connecting pipe into the body of the RTP pipe 3 respectively, then move the outer sleeve to a position flush with the end of the RTP pipe 3, and compress the outer sleeve to the designed diameter with a hydraulic compression device.
[0029] 4) Coating epoxy anti-corrosion paint on the outside of the outer sleeve.
Embodiment 2--1
[0030] Example 2--1 RTP pipe 3 connected to 316 steel pipe
[0031] 1) Put a 20# steel outer sleeve outside the RTP pipe 3;
[0032] 2) One end of the 316 connecting pipe with teeth is processed to form 3 pairs of sealing grooves, and three nitrile rubber sealing rings are respectively placed in the sealing grooves, and then coated with EVA hot melt adhesive on the part with teeth;
[0033] 3) Insert the toothed end of the connecting pipe into the RTP pipe 3, then move the outer sleeve to a position flush with the end of the RTP pipe 3, and compress the outer sleeve to the designed diameter with a hydraulic compression device.
[0034] 4) Weld the other end of the connecting pipe with the 316L steel pipe;
[0035] 5) Coating epoxy coal tar pitch anti-corrosion coating on the outer sleeve.
PUM
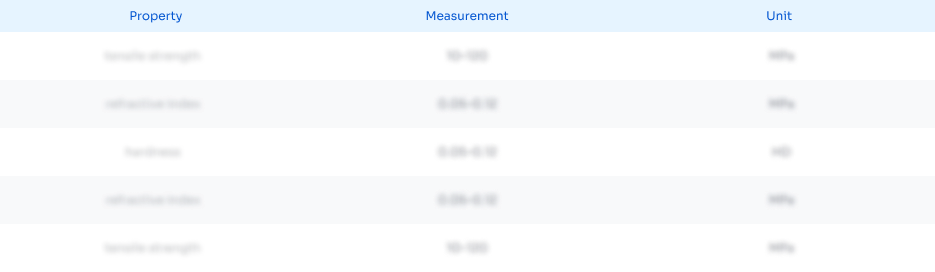
Abstract
Description
Claims
Application Information

- Generate Ideas
- Intellectual Property
- Life Sciences
- Materials
- Tech Scout
- Unparalleled Data Quality
- Higher Quality Content
- 60% Fewer Hallucinations
Browse by: Latest US Patents, China's latest patents, Technical Efficacy Thesaurus, Application Domain, Technology Topic, Popular Technical Reports.
© 2025 PatSnap. All rights reserved.Legal|Privacy policy|Modern Slavery Act Transparency Statement|Sitemap|About US| Contact US: help@patsnap.com