A kind of refining method of chlorothalonil raw material isophthalonitrile
A technology of isophthalonitrile and a purification method, which is applied in the field of purification of chlorothalonil raw material isophthalonitrile, can solve the problem that clean production and cost saving are not optimal, cannot be recycled, high temperature and vacuum degree, etc. problems, to achieve the effect of avoiding solid hazardous waste, less energy consumption, and mild process conditions
- Summary
- Abstract
- Description
- Claims
- Application Information
AI Technical Summary
Problems solved by technology
Method used
Image
Examples
Embodiment 1
[0032] Put 2000g of crude isophthalonitrile and 4000g of toluene into a 20L glass reaction kettle equipped with a reflux condenser and a tail gas absorption tower, heat to 80°C, add 107g of thionyl chloride dropwise, react for 5 hours, and use water and liquid caustic soda for the tail gas Two-stage absorption tower absorbs, cools to 10°C, slowly adds 500g of water to quench the reaction, stirs for 0.5 hours, and separates the liquid. extinction reaction. 6000 g of water was added to the organic phase, and the temperature was azeotropically distilled to 100°C. The distillate is layered, the organic phase is dried with anhydrous sodium sulfate, and the water phase is used for azeotropic distillation. After distillation, it is cooled to room temperature, filtered, centrifuged, the filtrate is used for azeotropic distillation, and the filter cake is dried under vacuum and reduced pressure. Obtained 1955g refined product of isophthalonitrile. GC detection of isophthalonitrile: 9...
Embodiment 2
[0034] Put 2000g of crude isophthalonitrile and 4000g of toluene into a 20L glass reaction kettle equipped with a reflux condenser and a tail gas absorption tower, heat to 80°C, add 121g of sulfuryl chloride dropwise, and react for 5 hours. Absorb in the absorption tower, cool to 10°C, slowly add 500g of water to quench the reaction, stir for 0.5 hours, separate the liquid, remove the three wastes from the lower layer of water, add 500g of water to the upper organic phase to wash and separate the liquid, and use the water phase to quench the reaction . 6000 g of water was added to the organic phase, and the temperature was azeotropically distilled to 100°C. The distillate is layered, the organic phase is dried with anhydrous sodium sulfate and used mechanically, the aqueous phase is used for azeotropic distillation, cooled to room temperature after distillation, filtered, centrifuged, the filtrate is used for azeotropic distillation, and the filter cake is dried under vacuum a...
Embodiment 3
[0036] Put 2000g of crude isophthalonitrile and 4000g of chlorobenzene into a 20L glass reactor equipped with a reflux condenser and a tail gas absorption tower, heat to 80°C, add 114g of oxalyl chloride dropwise, and react for 5 hours. Absorb in the absorption tower, cool to 10°C, slowly add 500g of water to quench the reaction, stir for 0.5 hours, separate the liquid, remove the three wastes from the lower layer of water, add 500g of water to the upper organic phase to wash and separate the liquid, and use the water phase for quenching reaction. 6000 g of water was added to the organic phase, and the temperature was azeotropically distilled to 100°C. The distillate is layered, the organic phase is dried with anhydrous sodium sulfate and used mechanically, the aqueous phase is used for azeotropic distillation, cooled to room temperature after distillation, filtered, centrifuged, the filtrate is used for azeotropic distillation, and the filter cake is dried under vacuum and re...
PUM
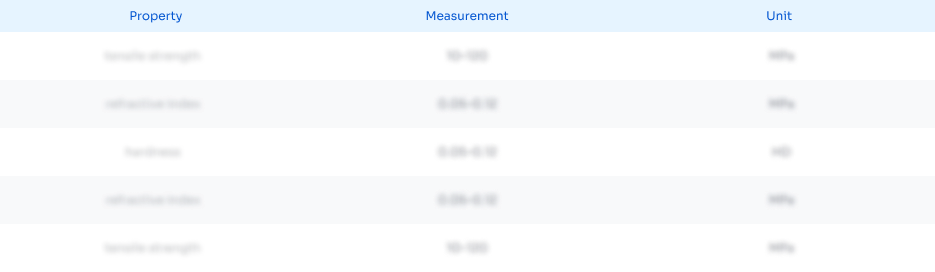
Abstract
Description
Claims
Application Information

- R&D
- Intellectual Property
- Life Sciences
- Materials
- Tech Scout
- Unparalleled Data Quality
- Higher Quality Content
- 60% Fewer Hallucinations
Browse by: Latest US Patents, China's latest patents, Technical Efficacy Thesaurus, Application Domain, Technology Topic, Popular Technical Reports.
© 2025 PatSnap. All rights reserved.Legal|Privacy policy|Modern Slavery Act Transparency Statement|Sitemap|About US| Contact US: help@patsnap.com