Natural fiber reinforced polylactic acid composite material having functionalized DOPO flame retardant and method for preparing same
A technology of natural fibers and composite materials, applied in the field of materials, can solve the problems of reducing the mechanical properties of materials, and achieve the effect of simple and effective preparation methods and mild process conditions
- Summary
- Abstract
- Description
- Claims
- Application Information
AI Technical Summary
Problems solved by technology
Method used
Image
Examples
Embodiment 1
[0033] (1) Dissolve 162g DOPO and 43.5g maleic acid in 800g ethanol solution, add to the reactor with stirrer and reflux condenser, stir and heat to 90°C, and reflux for 30 hours. Cool to room temperature and filter, collect the filter cake, and dry at 90°C for 10 hours to obtain the functionalized flame retardant DOPO.
[0034] (2) The flame retardant DOPO obtained in step (1) and polylactic acid, flax continuous long fiber, antioxidant phosphite tris(2,4-di-tert-butylphenyl) ester, anti-dripping agent polytetrafluoroethylene Vinyl fluoride was vacuum dried at 80°C for 16 hours to remove moisture;
[0035] (3) Take the dry 520g polylactic acid, 100g DOPO, 10g phosphite tris(2,4-di-tert-butylphenyl) ester, and 15g polytetrafluoroethylene obtained in step (2) and mix them uniformly in a high-speed mixer at 60°C Mix to obtain a mixed material.
[0036] (4) The mixture obtained in step (3) and 355g of flax fibers were added to a twin-screw extruder for extrusion, and the produc...
Embodiment 2
[0038] (1) Dissolve 162g DOPO and 118.5g itaconic acid in 600g ethanol solution, add to the reactor with stirrer and reflux condenser, stir and heat to 70°C, reflux for 40 hours. Cool to room temperature and filter, collect the filter cake, and dry at 100°C for 10 hours to obtain the functionalized flame retardant DOPO.
[0039] (2) The flame retardant DOPO and polylactic acid obtained in step (1), bamboo fiber with an aspect ratio of 5, the antioxidant tris(nonylphenyl phosphite), and the anti-dripping agent polytetrafluoroethylene were respectively heated at 60°C Dry under vacuum for 20 hours to remove moisture;
[0040] (3) Take 810g of dried polylactic acid obtained in step (2), 70g of flame retardant DOPO, 30g of tris(nonylphenyl phosphite), and 20g of polytetrafluoroethylene and mix them uniformly in a high-speed mixer at 70°C to obtain a mixture material.
[0041] (4) Add the mixture obtained in step (3) and 70g of bamboo fiber into a twin-screw extruder for extrusion...
Embodiment 3
[0043] (1) Dissolve 162g DOPO and 87g maleic acid in 1000g ethanol solution, add to the reactor with stirrer and reflux condenser, stir and heat to 100°C, reflux for 20 hours. Cool to room temperature and filter, collect the filter cake, and dry at 80°C for 12 hours to obtain the functionalized flame retardant DOPO.
[0044](2) The flame retardant DOPO and polylactic acid obtained in step (1), ramie yarn, the antioxidant triphenyl phosphite, and the anti-dripping agent polytetrafluoroethylene were vacuum-dried at 50°C for 24 hours to obtain remove moisture;
[0045] (3) Take 977g of dry polylactic acid obtained in step (2), 10g of flame retardant DOPO, 1g of triphenyl phosphite, and 1g of polytetrafluoroethylene and mix them uniformly in a high-speed mixer at 80°C to obtain a mixed material.
[0046] (4) Add the mixture obtained in step (3) and 10 g of ramie fiber into a twin-screw extruder for extrusion, and the product is cooled, pelletized, and dried to obtain a functional...
PUM
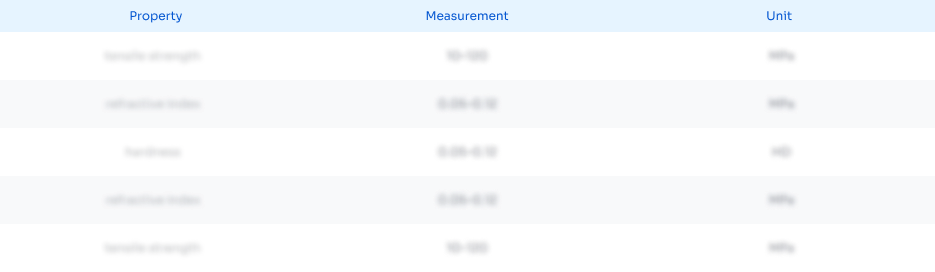
Abstract
Description
Claims
Application Information

- Generate Ideas
- Intellectual Property
- Life Sciences
- Materials
- Tech Scout
- Unparalleled Data Quality
- Higher Quality Content
- 60% Fewer Hallucinations
Browse by: Latest US Patents, China's latest patents, Technical Efficacy Thesaurus, Application Domain, Technology Topic, Popular Technical Reports.
© 2025 PatSnap. All rights reserved.Legal|Privacy policy|Modern Slavery Act Transparency Statement|Sitemap|About US| Contact US: help@patsnap.com