Aluminum oxide coated nickel-cobalt-manganese ternary positive electrode material, preparation method and application thereof
A positive electrode material and ternary material technology, which is applied in the field of alumina-coated nickel-cobalt-manganese ternary positive electrode materials and its preparation, can solve the problems of uneven surface reaction, poor thermal stability, and increased residual alkali on the surface. Good cycle performance and safety performance, preventing dissolution and reducing the effect of residual alkali
- Summary
- Abstract
- Description
- Claims
- Application Information
AI Technical Summary
Problems solved by technology
Method used
Image
Examples
Embodiment 1
[0035] (1) Add 1mol / L ammonia water to the container, place it in a water bath at 80°C for continuous heating and stirring, then slowly drop in 0.2mol / L aluminum nitrate solution to make the precipitate slowly form; react until the precipitate does not increase, Then add citric acid and 0.5mol / L nitric acid solution to it to slowly hydrolyze and peptize the precipitate, and continue to stir and age for 10-20h to obtain a clear AlOOH sol;
[0036] (2) Mix the precursor Ni with a molar ratio of 1:1.06 0.6 co 0.2 mn 0.2 (OH) 2 and battery-grade LiOH·H 2 O mixed together and ball milled, placed in an alumina ceramic crucible after mixing evenly, and sintered under the condition of compressed air, wherein the gas flow rate of sintering is 0.5-1.5L / min, and the heating rate of sintering is 5℃ / min, first keep it at 525°C for 3.5h, then raise the temperature to 840°C for 13h, and get black nickel-cobalt-manganese ternary material after calcination;
[0037] (3) Put the nickel-co...
Embodiment 2
[0040] (1) Add 1mol / L ammonia water to the container, place it in a water bath at 80°C for continuous heating and stirring, then slowly drop in 0.2mol / L aluminum nitrate solution to make the precipitate slowly form; react until the precipitate does not increase, Then add citric acid and 0.5mol / L nitric acid solution to it to slowly hydrolyze and peptize the precipitate, and continue to stir and age for 10-20h to obtain a clear AlOOH sol;
[0041] (2) Mix the precursor Ni with a molar ratio of 1:1.06 0.6 co 0.2 mn 0.2(OH) 2 and battery-grade LiOH·H 2 O are mixed together and ball milled, and placed in an alumina ceramic crucible after mixing evenly, and sintered at a high temperature under the condition of compressed air, wherein the sintering gas flow rate is 0.5-1.5L / min, and the sintering heating rate is 5°C / min, first hold at 525°C for 3.5h, then raise the temperature to 840°C for 13h, and obtain a black nickel-cobalt-manganese ternary material (referred to as uncoated...
Embodiment 3
[0045] A lithium-ion battery, comprising a housing and a positive pole placed in the housing, a negative pole, a diaphragm and an electrolyte, the diaphragm is located between the positive pole and the negative pole, the diaphragm is a glue-coated ceramic diaphragm, and the negative pole is artificial graphite, using 1.0mol / LiPF of L 6 The electrolytic solution of / EC+EMC+DEC (EC, EMC and DEC volume ratio is 3:5:2), and shell is square aluminum shell, and wherein positive pole is the coating material that embodiment 2 prepares. In order to compare the excellent performance of the coating material prepared by the method of the present invention when applied to the battery, another lithium ion battery was prepared, which had the same composition as the above battery, but with the uncoated material as the positive electrode. The high temperature expansion rate and normal temperature cycle performance of the above two batteries were detected, and the results were as follows: im...
PUM
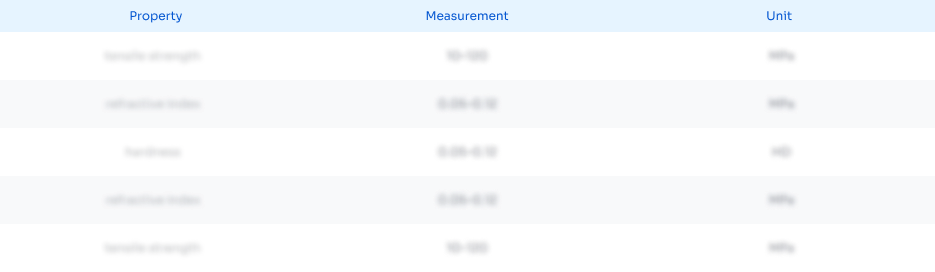
Abstract
Description
Claims
Application Information

- R&D Engineer
- R&D Manager
- IP Professional
- Industry Leading Data Capabilities
- Powerful AI technology
- Patent DNA Extraction
Browse by: Latest US Patents, China's latest patents, Technical Efficacy Thesaurus, Application Domain, Technology Topic, Popular Technical Reports.
© 2024 PatSnap. All rights reserved.Legal|Privacy policy|Modern Slavery Act Transparency Statement|Sitemap|About US| Contact US: help@patsnap.com