Pressurization alkali-boiling method for removing ceramic layer in thermal barrier coating
A technology for thermal barrier coatings and ceramic layers, which is applied in the field of pressurized alkali boiling for removing ceramic layers in thermal barrier coatings, can solve problems that have not been applied to the removal of thermal barrier coatings, and achieve high product quality consistency and convenience The effect of recoating and effective stripping
- Summary
- Abstract
- Description
- Claims
- Application Information
AI Technical Summary
Problems solved by technology
Method used
Image
Examples
Embodiment 1
[0051] 1) Prepare according to the designed alkali solution ratio, the masses of NaOH, KOH and deionized water are 100g, 100g and 200g respectively;
[0052] 2) Will figure 1 Place the parts in the high temperature and high pressure reactor, close the reactor and ensure the tightness of the reactor;
[0053] 3) Heat the alkali solution in the reaction kettle, control the heating temperature to 150±5°C, set the magnetic stirring speed to 1000rpm, and turn on the magnetic stirring to ensure the uniformity of the temperature of the alkali solution;
[0054] 4) After the temperature rises to the process temperature of 150±5°C, stop the magnetic stirring, and apply pulse pressure to the reaction kettle. The pulse pressure is set at 10-35MPa, and the pressurization time is controlled to be 30s;
[0055] 5) After the pressurization stops, start magnetic stirring for 30s; after the magnetic stirring ends, pressurize, and when pressurizing, turn off the magnetic stirring; each magneti...
Embodiment 2
[0065] 1) Prepare according to the designed alkali solution ratio, the masses of NaOH, KOH and deionized water are 100g, 500g and 4800g respectively;
[0066] 2) Will Figure 6 Place the parts in the high temperature and high pressure reactor, close the reactor and ensure the tightness of the reactor;
[0067] 3) Heat the alkali solution in the reaction kettle, control the heating temperature to 350±5°C, set the magnetic stirring speed to 2000rpm, and turn on the magnetic stirring to ensure the uniformity of the temperature of the alkali solution;
[0068] 4) After the temperature rises to the process temperature of 350±5°C, stop the magnetic stirring, and carry out pulse pressurization on the reaction kettle. The pulse pressure is set at 75-100MPa, and the pressurization time is controlled at 60s;
[0069] 5) After the pressurization stops, start magnetic stirring for 90s; after the magnetic stirring ends, pressurize, and when pressurizing, turn off the magnetic stirring; ea...
Embodiment 3
[0079] 1) Prepare according to the designed alkali solution ratio, the masses of NaOH, KOH and deionized water are 100g, 300g and 1600g respectively;
[0080] 2) Will figure 1 Place the parts in the high temperature and high pressure reactor, close the reactor and ensure the tightness of the reactor;
[0081] 3) Heat the alkali solution in the reaction kettle, control the heating temperature to 100±5°C, set the magnetic stirring speed to 500rpm, and turn on the magnetic stirring to ensure the uniformity of the temperature of the alkali solution;
[0082] 4) After the temperature rises to the process temperature of 100±5°C, stop the magnetic stirring, and pulse pressurize the reaction kettle. The pulse pressure is set at 36-74MPa, and the pressurization time is controlled at 90s;
[0083] 5) After the pressurization stops, start magnetic stirring for 50s; after the magnetic stirring ends, pressurize, and when pressurizing, turn off the magnetic stirring; each magnetic stirring...
PUM
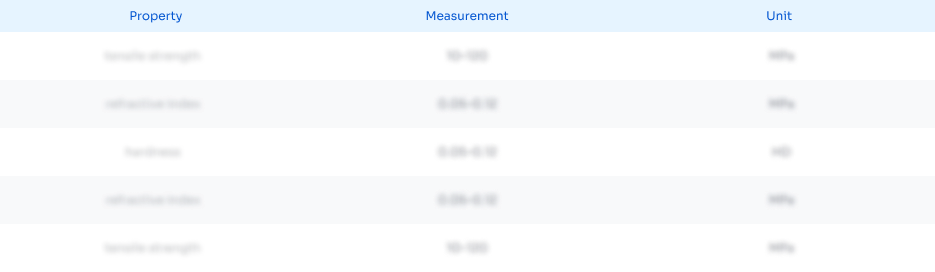
Abstract
Description
Claims
Application Information

- R&D
- Intellectual Property
- Life Sciences
- Materials
- Tech Scout
- Unparalleled Data Quality
- Higher Quality Content
- 60% Fewer Hallucinations
Browse by: Latest US Patents, China's latest patents, Technical Efficacy Thesaurus, Application Domain, Technology Topic, Popular Technical Reports.
© 2025 PatSnap. All rights reserved.Legal|Privacy policy|Modern Slavery Act Transparency Statement|Sitemap|About US| Contact US: help@patsnap.com