Method for manufacturing MOS transistor with germanium silicon source and drain
A MOS transistor, silicon germanium source-drain technology, applied in semiconductor/solid-state device manufacturing, electrical components, circuits, etc., can solve problems such as adverse effects on device performance, deformation of groove morphology, and loss of oxide layer.
- Summary
- Abstract
- Description
- Claims
- Application Information
AI Technical Summary
Problems solved by technology
Method used
Image
Examples
Embodiment Construction
[0036] like figure 1 Shown is the flow chart of the method of the embodiment of the present invention; Figure 2A to Figure 2D As shown, it is a device structure diagram in each step of the method of the embodiment of the present invention. The manufacturing method of the MOS transistor with silicon germanium source and drain in the embodiment of the present invention includes the following steps:
[0037] Step 1, such as Figure 2A As shown, a silicon substrate 101 is provided, a gate structure 105 is formed on the surface of the silicon substrate 101, side walls 106 are formed on the side of the gate structure 105, and the side walls 106 also extend to the gate The surface of the pole structure 105.
[0038] A shallow trench field oxygen is formed on the surface of the silicon substrate 101, an active region is isolated by the shallow trench field oxygen, and a MOS transistor is formed in the active region.
[0039] The MOS transistor with silicon germanium source and dra...
PUM
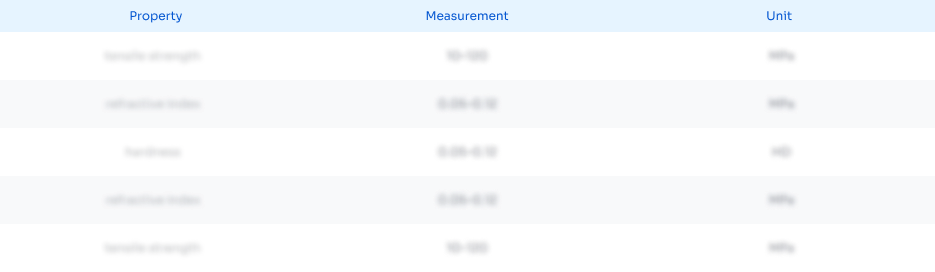
Abstract
Description
Claims
Application Information

- R&D Engineer
- R&D Manager
- IP Professional
- Industry Leading Data Capabilities
- Powerful AI technology
- Patent DNA Extraction
Browse by: Latest US Patents, China's latest patents, Technical Efficacy Thesaurus, Application Domain, Technology Topic, Popular Technical Reports.
© 2024 PatSnap. All rights reserved.Legal|Privacy policy|Modern Slavery Act Transparency Statement|Sitemap|About US| Contact US: help@patsnap.com