PA6-based thermal conductive composite material and preparation method thereof
A technology of thermally conductive composite material and thermally conductive filler, which is applied in the field of PA6-based thermally conductive composite material and its preparation, can solve the problems of poor mechanical properties of composite materials, difficult processing and molding, increased preparation cost, etc., and achieves good crystalline properties, thermal conductivity and mechanical properties. Excellent performance and high thermal conductivity
- Summary
- Abstract
- Description
- Claims
- Application Information
AI Technical Summary
Problems solved by technology
Method used
Examples
Embodiment 1
[0022] In the PA6-based heat-conducting composite material of this embodiment, the heat-conducting composite material is made of the following raw materials in parts by weight: the raw materials are dried in a vacuum oven and weighed in percentage by weight: PA6 / 350 g, HDPE / 150 g, oxidized Aluminum / 150 g, Aluminum Nitride / 300 g, Carbon Fiber / 25 g, Maleic Anhydride Compatibilizer / 25 g.
[0023] The PA6-based thermally conductive composite material of this embodiment is prepared by the following steps:
[0024] 1) Put the carbon fiber in a muffle furnace for calcination at 400°C for 8-12 hours, then soak it in acetone solution for 4-8 hours, filter, wash with deionized water several times, and place it in a vacuum drying oven at 80-100°C Dry in medium vacuum for 8-24 h, reflux concentrated nitric acid to oxidize the carbon fiber for 2-6 h, filter, wash with deionized water until the pH is equal to 7, dry in a vacuum oven at 80-100°C for 8-24 h, and oxidize the carbon fiber with ...
PUM
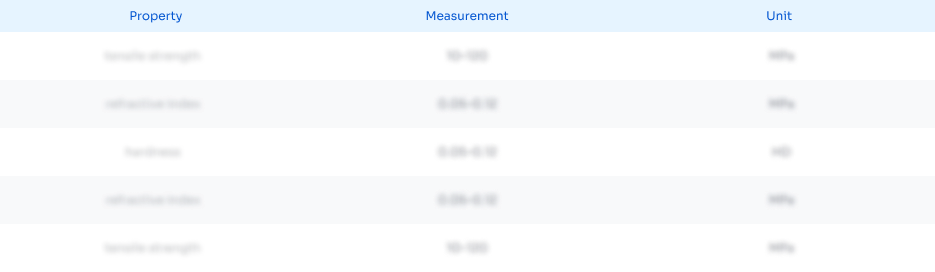
Abstract
Description
Claims
Application Information

- R&D
- Intellectual Property
- Life Sciences
- Materials
- Tech Scout
- Unparalleled Data Quality
- Higher Quality Content
- 60% Fewer Hallucinations
Browse by: Latest US Patents, China's latest patents, Technical Efficacy Thesaurus, Application Domain, Technology Topic, Popular Technical Reports.
© 2025 PatSnap. All rights reserved.Legal|Privacy policy|Modern Slavery Act Transparency Statement|Sitemap|About US| Contact US: help@patsnap.com