Biomass pellet fuel and preparation method thereof
A biomass particle and fuel technology, applied in the direction of biofuel, waste fuel, fuel, etc., can solve the problems of reduced output, ring die hole blockage, low pollution, etc., to improve molding rate and output, avoid ring die hole blockage, The effect of improving particle quality
- Summary
- Abstract
- Description
- Claims
- Application Information
AI Technical Summary
Problems solved by technology
Method used
Image
Examples
Embodiment 1
[0025] A biomass granular fuel prepared from the following raw materials in parts by weight: 71 parts of wheat straw, 46 parts of corn straw, 37 parts of wood chaff, 28 parts of fine sand, 17 parts of combustion enhancer, 3 parts of coal slime and additives 6 servings.
[0026] The additive is a binder, and the combustion aid includes one or both of magnesium chloride and sodium nitrate.
[0027] A preparation method of biomass pellet fuel, the specific steps are as follows:
[0028] (1) Crushing and mixing of raw materials: Weigh the following raw materials according to parts by weight: wheat straw, corn stalk, wood chaff, fine sand and coal slime, put them in a pulverizer and grind them, and mix them to make powder, fine sand and coal slime All are pre-screened to remove impurities;
[0029] (2) Sieving: the powder synthesized in the step (1) is sieved to remove impurities, and remove impurities that cause damage to mechanical equipment and affect the molding process, and ...
Embodiment 2
[0034] A biomass granular fuel prepared from the following raw materials in parts by weight: 72 parts of wheat straw, 47 parts of corn straw, 38 parts of wood bran, 29 parts of fine sand, 18 parts of combustion enhancer, 4 parts of coal slime and additives 7 servings.
[0035] The additive is a binder, and the combustion aid includes one or both of magnesium chloride and sodium nitrate.
[0036] A preparation method of biomass pellet fuel, the specific steps are as follows:
[0037] (1) Crushing and mixing of raw materials: Weigh the following raw materials according to parts by weight: wheat straw, corn stalk, wood chaff, fine sand and coal slime, put them in a pulverizer and grind them, and mix them to make powder, fine sand and coal slime All are pre-screened to remove impurities;
[0038] (2) Sieving: the powder synthesized in the step (1) is sieved to remove impurities, and remove impurities that cause damage to mechanical equipment and affect the molding process, and t...
Embodiment 3
[0043] A biomass granular fuel prepared from the following raw materials in parts by weight: 73 parts of wheat straw, 48 parts of corn straw, 39 parts of wood chaff, 30 parts of fine sand, 19 parts of combustion enhancer, 5 parts of coal slime and additives 8 servings.
[0044] The additive is a binder, and the combustion aid includes one or both of magnesium chloride and sodium nitrate.
[0045] A preparation method of biomass pellet fuel, the specific steps are as follows:
[0046] (1) Crushing and mixing of raw materials: Weigh the following raw materials according to parts by weight: wheat straw, corn stalk, wood chaff, fine sand and coal slime, put them in a pulverizer and grind them, and mix them to make powder, fine sand and coal slime All are pre-screened to remove impurities;
[0047] (2) Sieving: the powder synthesized in the step (1) is sieved to remove impurities, and remove impurities that cause damage to mechanical equipment and affect the molding process, and ...
PUM
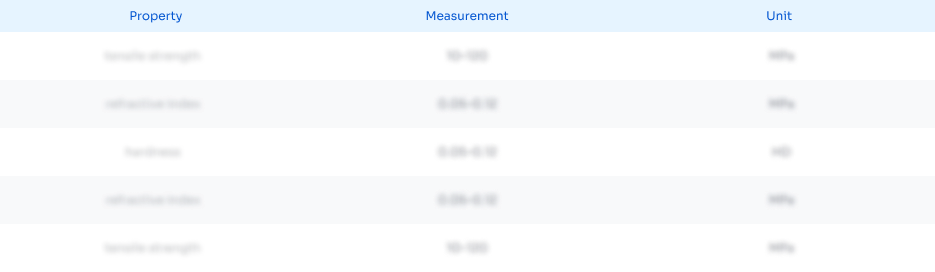
Abstract
Description
Claims
Application Information

- R&D
- Intellectual Property
- Life Sciences
- Materials
- Tech Scout
- Unparalleled Data Quality
- Higher Quality Content
- 60% Fewer Hallucinations
Browse by: Latest US Patents, China's latest patents, Technical Efficacy Thesaurus, Application Domain, Technology Topic, Popular Technical Reports.
© 2025 PatSnap. All rights reserved.Legal|Privacy policy|Modern Slavery Act Transparency Statement|Sitemap|About US| Contact US: help@patsnap.com