A sorting process for processing magnetic red mixed ore based on iron mineral embedding particle size
A technology of iron minerals and particle size, applied in the field of mineral processing, can solve the problems of increased chemical pollution, low sorting efficiency, increased sorting cost, etc., achieve the effects of reducing over-grinding, improving technical indicators, and realizing energy saving and consumption reduction
- Summary
- Abstract
- Description
- Claims
- Application Information
AI Technical Summary
Problems solved by technology
Method used
Image
Examples
Embodiment Construction
[0029] The present invention will be further described below in conjunction with drawings and embodiments.
[0030] Such as figure 1 As shown, according to the characteristics of high magnetic iron content in raw ore and uneven particle size distribution of iron minerals in maghetic mixed iron ore, the present invention adopts the grinding and separation process of segmental grinding, segmental extraction and segmental tailing To sort this type of ore.
[0031] A sorting process of the present invention for processing magnetic-red mixed ore based on iron mineral embedding particle size, including feeding mixed ore with an iron grade of 28% and a magnetic iron distribution rate of 75% into a first-stage grinding and a primary cyclone A section of closed-circuit grinding operation formed to obtain a primary graded overflow product with a particle size of -200 mesh and a content of 65%; it is characterized in that: it also includes the following operations:
[0032] A section o...
PUM
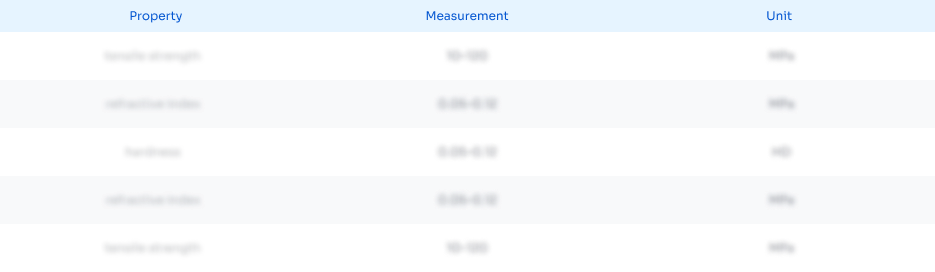
Abstract
Description
Claims
Application Information

- R&D
- Intellectual Property
- Life Sciences
- Materials
- Tech Scout
- Unparalleled Data Quality
- Higher Quality Content
- 60% Fewer Hallucinations
Browse by: Latest US Patents, China's latest patents, Technical Efficacy Thesaurus, Application Domain, Technology Topic, Popular Technical Reports.
© 2025 PatSnap. All rights reserved.Legal|Privacy policy|Modern Slavery Act Transparency Statement|Sitemap|About US| Contact US: help@patsnap.com