Anti-cracking composite ceramic
A technology of composite ceramics and base materials, applied in the field of ceramic processing, can solve problems such as cracking, failure to meet performance requirements, and low yield, and achieve the effects of cost reduction, good strength, and good adsorption
- Summary
- Abstract
- Description
- Claims
- Application Information
AI Technical Summary
Problems solved by technology
Method used
Examples
Embodiment 1
[0026] A kind of anti-cracking composite ceramics, comprising bottom base material, middle base material and surface base material,
[0027] The bottom base material is made of the following raw materials in parts by weight: 58 parts of cancryptite, 13 parts of alumina, 10 parts of zirconium silicate, 4.2 parts of zinc oxide, and 9 parts of clay;
[0028] The middle base material is made of the following raw materials in parts by weight: 48 parts of kaolin, 11 parts of barium carbonate, 18 parts of orthoclase, 6 parts of mica powder, 7.5 parts of sodium carboxymethyl cellulose, and 6.2 parts of nano-titanium dioxide;
[0029] The surface base material is made of the following raw materials in parts by weight: 14 parts of potassium feldspar, 92 parts of quartz stone, 8 parts of aluminum silicate, 6.5 parts of montmorillonite, and 4 parts of nano-titanium dioxide.
[0030] The zirconium silicate in the base material of the bottom layer is treated by the following method, (1) soa...
Embodiment 2
[0042] A kind of anti-cracking composite ceramics, comprising bottom base material, middle base material and surface base material,
[0043] The bottom base material is made of the following raw materials in parts by weight: 60 parts of cancryptite, 13 parts of alumina, 9 parts of zirconium silicate, 4 parts of zinc oxide, and 9 parts of clay;
[0044] The middle base material is made of the following raw materials in parts by weight: 48 parts of kaolin, 9 parts of barium carbonate, 17 parts of orthoclase, 6 parts of mica powder, 8 parts of sodium carboxymethyl cellulose, and 6 parts of nano-titanium dioxide;
[0045] The surface base material is made of the following raw materials in parts by weight: 13 parts of potassium feldspar, 95 parts of quartz stone, 8 parts of aluminum silicate, 6 parts of montmorillonite, and 4 parts of nano titanium dioxide.
[0046] The processing mode and specific preparation method of each raw material are the same as in Example 1.
Embodiment 3
[0048] Compared with Example 1, zirconium silicate was directly added without treatment.
[0049] Experiment 1
[0050] In order to verify the influence of raw materials on the performance of composite ceramics, the applicant has carried out relevant verification tests and set up the following control tests:
PUM
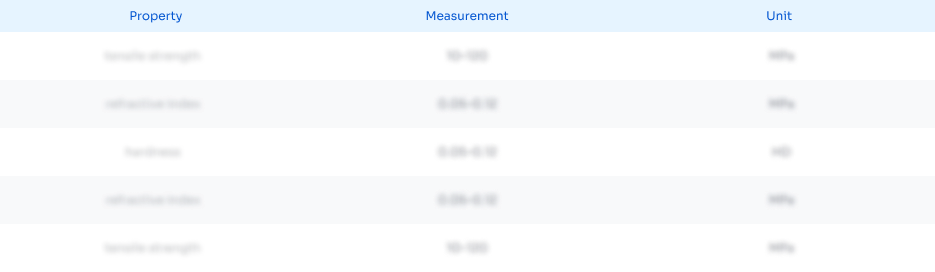
Abstract
Description
Claims
Application Information

- R&D Engineer
- R&D Manager
- IP Professional
- Industry Leading Data Capabilities
- Powerful AI technology
- Patent DNA Extraction
Browse by: Latest US Patents, China's latest patents, Technical Efficacy Thesaurus, Application Domain, Technology Topic, Popular Technical Reports.
© 2024 PatSnap. All rights reserved.Legal|Privacy policy|Modern Slavery Act Transparency Statement|Sitemap|About US| Contact US: help@patsnap.com