Preparation method of low-oxygen vanadium-nitrogen alloy
A technology of oxygen-vanadium-nitrogen alloy and nitrogen alloy, applied in the field of preparation of low-oxygen vanadium-nitrogen alloy, which can solve the problems of incomplete reduction of vanadium oxide, affecting the use effect of steel, and high residual oxygen content in products.
- Summary
- Abstract
- Description
- Claims
- Application Information
AI Technical Summary
Problems solved by technology
Method used
Examples
Embodiment 1
[0024] The production method of the low-oxygen vanadium-nitrogen alloy of the present embodiment may further comprise the steps:
[0025] Step 1: Add powdery vanadium compound and carbonaceous powder into a vacuum induction heating furnace, carry out carbonization reaction at a vacuum of 100Pa and a temperature of 1100°C-1400°C, keep the temperature for 3-5 hours, then cool to room temperature, and leave The vanadium carbide after charging is packed with the first sealed barrel, and nitrogen protection is passed into the sealed barrel.
[0026] Step 2: Import the vanadium carbide in the sealed barrel into the atmosphere-protected tilting wet mill, and add forming agent and wet grinding medium into the tilting wet mill for wet ball milling. The tilting wet mill Internal nitrogen protection, after ball milling in a tilting wet mill for 4-6 hours, mix evenly to form a vanadium carbide slurry, and pour it into the second sealed barrel.
[0027] Step 3: Place the second sealed bar...
Embodiment 2
[0037] This embodiment includes the following steps:
[0038] Step 1: Add vanadium pentoxide and graphite powder according to the ratio of 100 parts by weight: 27 parts into a vacuum induction heating furnace, carry out carbonization reaction at a vacuum degree of 100 Pa, and a temperature of 1100 ° C, and keep warm for 5 hour, then cooled to room temperature, the vanadium carbide after the discharge is packed with the first sealed barrel, and nitrogen protection is passed into the sealed barrel.
[0039] Step 2: Import the vanadium carbide in the sealed barrel into an atmosphere-protected tilting wet mill, and add molding agent paraffin and wet grinding medium anhydrous ethanol into the tilting wet mill for wet ball milling. Nitrogen protection in the type wet mill, after ball milling by the tilting type wet mill for 4 hours, mix evenly to form a vanadium carbide slurry, and pour it into the second sealed barrel.
[0040] Step 3: Place the second sealed barrel containing the...
Embodiment 3
[0044] Step 1: Get ammonium metavanadate and charcoal powder according to the proportioning ratio of parts by weight of 100 parts: 29 parts, and mix 0.8 part of reduced iron powder, the average particle size of reduced iron powder is 30 microns, join above raw material in In the vacuum induction heating furnace, the carbonization reaction is carried out at a vacuum degree of 100 Pa and a temperature of 1400 ° C. The temperature is kept for 3 hours, and then cooled to room temperature. The discharged vanadium carbide is packed in the first sealed barrel, and the sealed barrel is passed into Nitrogen protection.
[0045] Step 2: Introduce the vanadium carbide in the sealed barrel into an atmosphere-protected tilting wet mill, and add molding agent polyethylene glycol (PEG) and wet grinding medium acetone into the tilting wet mill for wet grinding Ball milling, nitrogen protection in the tilting wet mill, after ball milling in the tilting wet mill for 6 hours, mix evenly to form ...
PUM
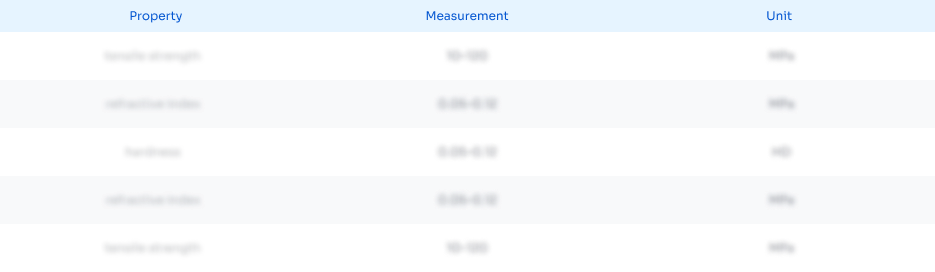
Abstract
Description
Claims
Application Information

- R&D
- Intellectual Property
- Life Sciences
- Materials
- Tech Scout
- Unparalleled Data Quality
- Higher Quality Content
- 60% Fewer Hallucinations
Browse by: Latest US Patents, China's latest patents, Technical Efficacy Thesaurus, Application Domain, Technology Topic, Popular Technical Reports.
© 2025 PatSnap. All rights reserved.Legal|Privacy policy|Modern Slavery Act Transparency Statement|Sitemap|About US| Contact US: help@patsnap.com