A kind of austenitic stainless steel refining method
A technology of austenitic stainless steel and molten steel, applied in the field of stainless steel refining, can solve the problems of long smelting time, high production cost, and low production efficiency, and achieve the effects of shortening smelting time, increasing service life, and reducing ferrosilicon consumption
- Summary
- Abstract
- Description
- Claims
- Application Information
AI Technical Summary
Problems solved by technology
Method used
Examples
Embodiment 1
[0026] The process adopts EAF electric arc furnace + AOD refining dual process.
[0027] The 316L steel produced contains the following components by weight per 100 parts: Cr: 16.5-16.8 parts, Ni: 10.02-10.1 parts, Mo: 2.02-2.08 parts, C: 0.012-0.028 parts, P: 0.025- 0.045 parts, S: 0.001-0.03 parts, Si: 0.01-0.8 parts, Mn: 0.1-1.2 parts, and the rest are Fe and unavoidable impurities.
[0028] Since AOD stainless steel refining cannot remove P, the P content of steelmaking raw materials is strictly controlled.
[0029] a. Melting steel: put scrap steel into EAF electric arc furnace in three batches as steelmaking raw material, add 40% steelmaking raw material in the first batch, wait for the temperature of molten steel in EAF electric arc furnace to reach 1600 ℃, then add 20% of the second batch Steel-making raw materials, when the temperature of molten steel in the EAF electric arc furnace reaches 1600°C, add 40% steel-making raw materials in the third batch; spray a mixtur...
Embodiment 2
[0037] The process adopts EAF electric arc furnace + AOD refining dual process.
[0038] The 316L steel produced contains the following components by weight per 100 parts: Cr: 16.5-16.8 parts, Ni: 10.02-10.1 parts, Mo: 2.02-2.08 parts, C: 0.012-0.028 parts, P: 0.025- 0.045 parts, S: 0.001-0.03 parts, Si: 0.01-0.8 parts, Mn: 0.1-1.2 parts, and the rest are Fe and unavoidable impurities.
[0039] a. Steel melting: use scrap steel as raw material for steelmaking, add it to EAF electric arc furnace in four batches, add 40%, 20%, 20% and 20% of steelmaking raw material in each batch, and the temperature of molten steel reaches 1600 before each feeding. ℃; spray a mixture of 60% carbon powder and 40% aluminum powder from the furnace door, and melt the steelmaking raw materials into molten steel to obtain product A;
[0040] b. Ingredients: add 350KG lime, 230KG carbon balls and 300KG ferrosilicon to product A, take a sample of molten steel for spectral analysis, adjust the composit...
Embodiment 3
[0047] The process adopts EAF electric arc furnace + AOD refining dual process.
[0048] The 304L steel produced contains the following components by weight per 100 parts: Cr: 18.5-19.5 parts, Ni: 8.05-11.8 parts, C: 0.012-0.032 parts, P: 0.025-0.045 parts, S: 0.002- 0.03 parts, Si: 0.1-0.8 parts, Mn: 0.3-1.6 parts, and the rest are Fe and unavoidable impurities.
[0049] a. Steel melting: use scrap steel as raw material for steelmaking, add it to EAF electric arc furnace in four batches, add 40%, 20%, 20% and 20% of steelmaking raw material in each batch, and the temperature of molten steel reaches 1600 before each feeding. ℃; spray a mixture of 60% carbon powder and 40% aluminum powder from the furnace door, and melt the steelmaking raw materials into molten steel to obtain product A;
[0050] b. Ingredients: add 330KG lime, 220KG carbon balls and 280KG ferrosilicon to product A, take a sample of molten steel for spectral analysis, adjust the composition according to the an...
PUM
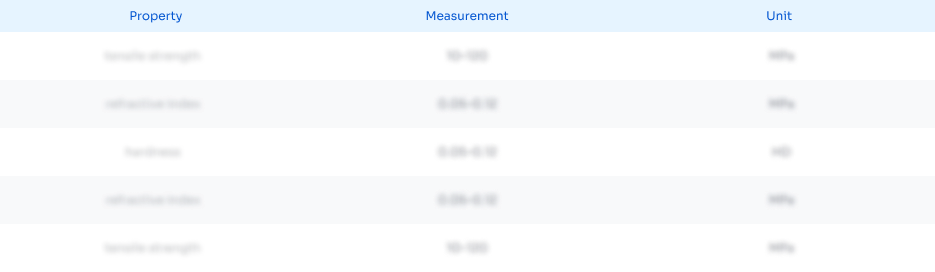
Abstract
Description
Claims
Application Information

- R&D Engineer
- R&D Manager
- IP Professional
- Industry Leading Data Capabilities
- Powerful AI technology
- Patent DNA Extraction
Browse by: Latest US Patents, China's latest patents, Technical Efficacy Thesaurus, Application Domain, Technology Topic, Popular Technical Reports.
© 2024 PatSnap. All rights reserved.Legal|Privacy policy|Modern Slavery Act Transparency Statement|Sitemap|About US| Contact US: help@patsnap.com