A kind of method that utilizes asbestos tailings to prepare porous silica
A technology of porous silica and asbestos tailings, which is applied in the directions of silica, silica, chemical instruments and methods, etc., can solve the problem of easily corroded containers by acid solutions, easily corroded containers by alkaline solutions, low magnesia leaching rate, etc. problems, to achieve the effect of easy promotion and application, low equipment requirements and low cost
- Summary
- Abstract
- Description
- Claims
- Application Information
AI Technical Summary
Problems solved by technology
Method used
Image
Examples
Embodiment 1
[0044] A method for preparing porous silicon dioxide from asbestos tailings, comprising the steps of:
[0045] (1) Ball milling. Take an asbestos tailings in southern Shaanxi, crush them in a ball mill with a rotating speed of 220r / min, and mill them for 8 hours to obtain tailings powder with a particle size of 4.0um to 534.9um; among them, the asbestos tailings include magnesium oxide 40%~42%, silicon dioxide 43%~45%, iron oxide 3%~5%, nickel oxide 0.45%~0.55%;
[0046] (2) Mixing, filtering the above tailings powder with a 400-mesh sieve, and then mixing it with ammonium bisulfate evenly to prepare a powder mixture with a mass ratio of tailings powder and ammonium bisulfate of 1:2.93;
[0047] (3) Roasting, the above powder mixture is moved into a corundum crucible, and then reacted in a box-type resistance furnace at a temperature of 500 ° C for 2.5 hours to obtain powder clinker;
[0048] (4) Dissolution, dissolve the above powder clinker with deionized water to obtain a ...
Embodiment 2
[0052] A method for preparing porous silicon dioxide from asbestos tailings, comprising the steps of:
[0053] (1) Ball milling, pulverize the asbestos tailings in a ball mill with a rotational speed of 240r / min, and ball mill for 7.5 hours to obtain tailings powder with a particle size of 4.0um to 534.9um;
[0054] (2) Mixing, the above tailings powder is filtered through a stainless steel metal screen with a pore size of 0.0374mm, and then mixed with ammonium bisulfate to obtain a powder mixture with a mass ratio of tailings powder and ammonium bisulfate of 1:3.1;
[0055] (3) Roasting, move the above powder mixture into a corundum crucible, and then react in a box-type resistance furnace at a temperature of 530°C for 2.3 hours to obtain powder clinker;
[0056] (4) Dissolution, dissolving the above powder clinker with deionized water 5.5 times the mass of powder clinker to obtain a clinker turbid liquid; Alkaline clinker turbid liquid;
[0057] (5) Separation, using a Buc...
Embodiment 3
[0060] A method for preparing porous silicon dioxide from asbestos tailings, comprising the steps of:
[0061] (1) Ball milling, pulverize the cotton tailings in a ball mill with a rotating speed of 210r / min, and ball mill for 8.5 hours to obtain tailings powder with a particle size of 4.0um to 534.9um;
[0062] (2) Mixing, filter the above tailings powder with a sieve with a pore size less than 0.0374mm, and then mix it evenly with ammonium bisulfate to prepare a powder mixture with a mass ratio of tailings powder and activator ammonium bisulfate of 1:3.3 ;
[0063] (3) Roasting, move the above powder mixture into a corundum crucible, and then react in a box-type resistance furnace at a temperature of 470°C for 3 hours to obtain powder clinker;
[0064] (4) Dissolution, dissolving the above powder clinker with deionized water with 6 times the mass of powder clinker to obtain a clinker turbid liquid; Alkaline clinker turbid liquid;
[0065] (5) Separation, using a Buchner f...
PUM
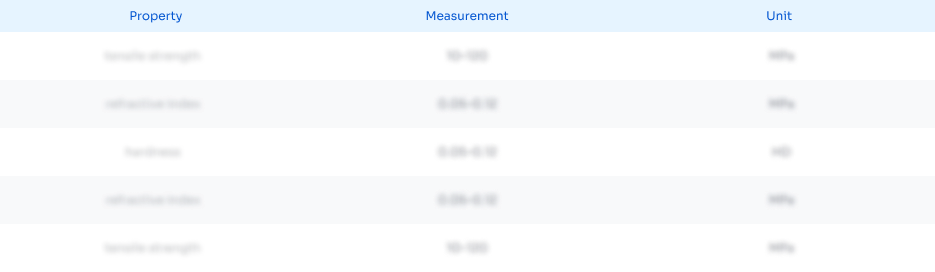
Abstract
Description
Claims
Application Information

- R&D
- Intellectual Property
- Life Sciences
- Materials
- Tech Scout
- Unparalleled Data Quality
- Higher Quality Content
- 60% Fewer Hallucinations
Browse by: Latest US Patents, China's latest patents, Technical Efficacy Thesaurus, Application Domain, Technology Topic, Popular Technical Reports.
© 2025 PatSnap. All rights reserved.Legal|Privacy policy|Modern Slavery Act Transparency Statement|Sitemap|About US| Contact US: help@patsnap.com