A kind of smelting method of chromium molybdenum steel for hydrogen equipment
A smelting method and a technology for hydrogenation equipment, which are applied in the smelting field of chromium-molybdenum steel for hydrogenation equipment, can solve the problems of harsh use conditions and the tendency of high-temperature tempering and embrittlement of chromium-molybdenum steel to increase, and reduce nitrogen content and hydrogen The effect of content
- Summary
- Abstract
- Description
- Claims
- Application Information
AI Technical Summary
Problems solved by technology
Method used
Examples
Embodiment 1
[0023] This embodiment is a method for smelting 12Cr2Mo1R hydrogen-prone chromium-molybdenum steel, and the production steps include:
[0024] (1) Hot metal pretreatment: The composition of hot metal is C=4.66%, Si=0.35%, Mn=0.34%, S=0.043%, P=0.136%, Sn=0.004%, As=0.0071% by weight percentage; using KR Stirring desulfurization, adding 0.46kg / t magnesium powder, removing the blast furnace slag before desulfurization, removing the desulfurization slag after desulfurization, the thickness of the slag layer after removing the slag meets the requirements of ≤25mm, and then measuring the temperature and sampling, the sulfur content in the hot metal is 0.0032 %, the temperature of molten iron is 1313°C;
[0025] (2) Converter: Dephosphorization by double slag method, adding 12.4t of high-quality steel scrap, 5.2t of lime, 1t of light-burned dolomite, 1.8t of fluorite, and 1.6t of iron ore for slagging, of which the amount of molten iron loaded It is 130.5t; the main blowing oxygen ...
Embodiment 2
[0031] This embodiment is a method for smelting 15CrMoR hydrogen-prone chromium-molybdenum steel, and the production steps include:
[0032] (1) (1) Hot metal pretreatment: The composition of hot metal by weight percentage is C=4.52%, Si=0.46%, Mn=0.40%, S=0.048%, P=0.147%, Sn=0.003%, As=0.0067% ; Use KR stirring method for desulfurization, add 0.25kg / t magnesium powder and 3.6kg / t lime, remove the blast furnace slag before desulfurization, remove the desulfurization slag after desulfurization, the thickness of the slag layer after removal meets the requirements of ≤25mm, and then measure Warm sampling, the sulfur content of molten iron is 0.0020%, and the temperature of molten iron is 1278°C;
[0033] (2) Converter: Dephosphorization by double slag method, adding 14.6t of high-quality steel scrap, 4.6t of lime, 1.5t of light-burned dolomite, 1.5t of fluorite, and 1.8t of iron ore for slagging, among which molten iron is put into The volume is 132.7t; the main blowing oxygen ...
PUM
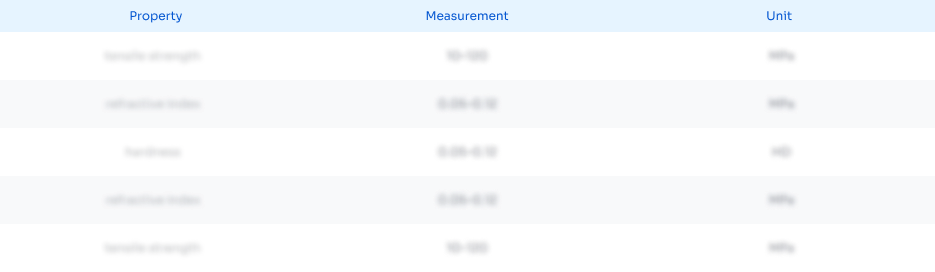
Abstract
Description
Claims
Application Information

- R&D
- Intellectual Property
- Life Sciences
- Materials
- Tech Scout
- Unparalleled Data Quality
- Higher Quality Content
- 60% Fewer Hallucinations
Browse by: Latest US Patents, China's latest patents, Technical Efficacy Thesaurus, Application Domain, Technology Topic, Popular Technical Reports.
© 2025 PatSnap. All rights reserved.Legal|Privacy policy|Modern Slavery Act Transparency Statement|Sitemap|About US| Contact US: help@patsnap.com