Channel-type induction-heating ladle device and heating method
An induction heating and channel-type technology, which is applied in metal processing equipment, casting molten material containers, casting equipment, etc., can solve the problems that the resistance heating method has not been developed and promoted, the heating rate is difficult, and the heating efficiency is low, etc., to achieve shortening Production cycle, simple design, and the effect of improving efficiency
- Summary
- Abstract
- Description
- Claims
- Application Information
AI Technical Summary
Problems solved by technology
Method used
Image
Examples
Embodiment
[0042] A channel type induction heating ladle device and heating method, such as Figure 1~Figure 11 As shown, it includes ladle 1, iron core 2, coil 3, water-cooled or air-cooled device 4, refractory material layer 5, steel shell 6, channel 7, slit 8, and ladle cover 9. Among them, the ladle 1 has a through channel 7; the iron core 2 passes through the channel 7 and surrounds one side of the ladle 1; the coil 3 is wound on the iron core 2 and is located outside the ladle 1; the ladle cover 9 covers the top of the ladle 1 .
[0043] The material of the iron core 2 is silicon steel sheet, and the gap between the iron core 2 and the channel 7 is filled with refractory material.
[0044] The material of the coil 3 is copper, and the heating power of the coil 3 is 500 kW.
[0045] The axis of the coil 3 is perpendicular to the axis of the iron core 2.
[0046] The water-cooled or air-cooled device 4 is to reduce the temperature of the coil 3 after power-on, protect the coil 3, and preve...
PUM
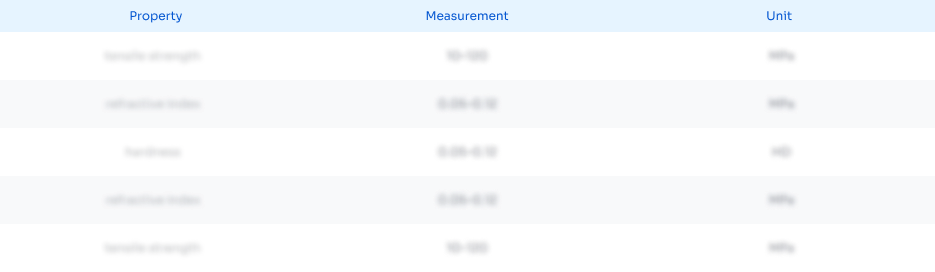
Abstract
Description
Claims
Application Information

- Generate Ideas
- Intellectual Property
- Life Sciences
- Materials
- Tech Scout
- Unparalleled Data Quality
- Higher Quality Content
- 60% Fewer Hallucinations
Browse by: Latest US Patents, China's latest patents, Technical Efficacy Thesaurus, Application Domain, Technology Topic, Popular Technical Reports.
© 2025 PatSnap. All rights reserved.Legal|Privacy policy|Modern Slavery Act Transparency Statement|Sitemap|About US| Contact US: help@patsnap.com