Method for improving flame retardant property of polyurethane foam
A technology of polyurethane foam and flame retardant properties, applied in the field of foam plastic modification, can solve the problems of large amount of flame retardants, poor compatibility between flame retardants and substrates, and inability to effectively exert flame retardant effects, etc., to achieve Improve flame retardant performance and enhance the effect of mechanical properties
- Summary
- Abstract
- Description
- Claims
- Application Information
AI Technical Summary
Problems solved by technology
Method used
Examples
Embodiment 1
[0035] 1) Wash the polyurethane foam, immerse it in absolute ethanol for immersion treatment in an environment of 0.3 atm, take it out after it no longer generates bubbles, and then immerse it in decahydronaphthalene for 5 minutes;
[0036] 2) prepare pretreatment liquid, its step is:
[0037] a) Add methyl p-toluenesulfonate and 2-ethyl-4,5-dihydrooxazoline to anhydrous acetonitrile to prepare a mixed solution, the concentration of methyl p-toluenesulfonate in the mixed solution is 0.2mmol / L , the concentration of 2--ethyl-4,5-dihydrooxazoline is 1.05mmol / L, the mixture is ultrasonically oscillated for 20min, then heated at 80°C for 48h, and the solvent is evaporated to dryness to obtain a powder ;
[0038] b) Add the powder obtained in step a) into 18wt% hydrogen chloride solution, the mass ratio of the used powder to the hydrogen chloride solution is 15:18, stir for 15 minutes, then place it at 100°C for 24 hours, and rotate to evaporate Slowly add saturated sodium hydrox...
Embodiment 2
[0045] 1) Washing the polyurethane foam, immersing it in absolute ethanol in an environment of 0.5 atm for immersion treatment, taking it out after it no longer generates bubbles, and then immersing it in decahydronaphthalene for 10 minutes;
[0046] 2) prepare pretreatment liquid, its step is:
[0047] a) Add methyl p-toluenesulfonate and 2-ethyl-4,5-dihydrooxazoline to anhydrous acetonitrile to prepare a mixed solution, the concentration of methyl p-toluenesulfonate in the mixed solution is 0.3mmol / L , the concentration of 2--ethyl-4,5-dihydrooxazoline is 1.35mmol / L, the mixture is ultrasonically oscillated for 25min, then heated at 85°C for 50h, and the solvent is evaporated to dryness to obtain a powder ;
[0048] b) Add the powder obtained in step a) into 19wt% hydrogen chloride solution, the mass ratio of the used powder to the hydrogen chloride solution is 15:22, stir for 20 minutes, place it at 115°C for 26 hours, and rotate to evaporate Slowly add saturated sodium h...
Embodiment 3
[0055] 1) Washing the polyurethane foam, immersing it in absolute ethanol in an environment of 0.35 atm for immersion treatment, taking it out after it no longer generates bubbles, and then immersing it in decahydronaphthalene for 10 minutes;
[0056] 2) prepare pretreatment liquid, its step is:
[0057] a) Add methyl p-toluenesulfonate and 2-ethyl-4,5-dihydrooxazoline to anhydrous acetonitrile to prepare a mixed solution, the concentration of methyl p-toluenesulfonate in the mixed solution is 0.3mmol / L , the concentration of 2--ethyl-4,5-dihydrooxazoline is 1.05mmol / L, the mixture is ultrasonically oscillated for 25min, then heated at 80°C for 48h, and the solvent is evaporated to dryness to obtain a powder ;
[0058] b) Add the powder obtained in step a) into 18t% hydrogen chloride solution, the mass ratio of the powder used to the hydrogen chloride solution is 15:20, stir for 20 minutes, place it at 110°C for 24 hours, and rotate to evaporate Slowly add saturated sodium h...
PUM
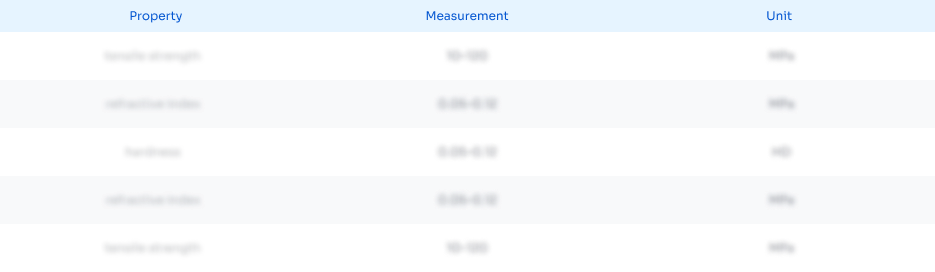
Abstract
Description
Claims
Application Information

- R&D Engineer
- R&D Manager
- IP Professional
- Industry Leading Data Capabilities
- Powerful AI technology
- Patent DNA Extraction
Browse by: Latest US Patents, China's latest patents, Technical Efficacy Thesaurus, Application Domain, Technology Topic, Popular Technical Reports.
© 2024 PatSnap. All rights reserved.Legal|Privacy policy|Modern Slavery Act Transparency Statement|Sitemap|About US| Contact US: help@patsnap.com