Rolling method for producing wide-width packaging aluminum plate
An aluminum-clad, wide-width technology is applied in the rolling field of producing wide-width aluminum-clad plates, which can solve the problems of lower production efficiency, increase of production process, and inconvenience of industrial production, and achieve improved production efficiency, shortened processing flow, and improved surface quality Effect
- Summary
- Abstract
- Description
- Claims
- Application Information
AI Technical Summary
Problems solved by technology
Method used
Image
Examples
Embodiment Construction
[0048] Hereinafter, the preferred embodiments of the present invention will be described in detail with reference to the accompanying drawings.
[0049] The rolling method for producing a wide-width clad aluminum plate of this embodiment mainly includes the following steps:
[0050] (1) Select materials and make composite ingots.
[0051] 11) Choose 2024 alloy as the core material ingot, the size is 500×2080×4600mm, and choose 1050 alloy as the skin ingot; the 2024 core material ingot is milled and the head and tail are cut off, and the size after sawing and milling is 450×2040 ×4000mm.
[0052] 12) According to the requirements of the AMS4462 standard cladding ratio, the 1050 alloy ingot as the skin material is rolled into a 25mm thick plate by the conventional rolling process.
[0053] 13) According to the width of the skin material is 150-250mm narrower than the core material, and the length is 450-550mm narrower, the rolled thick plate is cut to length into two pieces of skin mater...
PUM
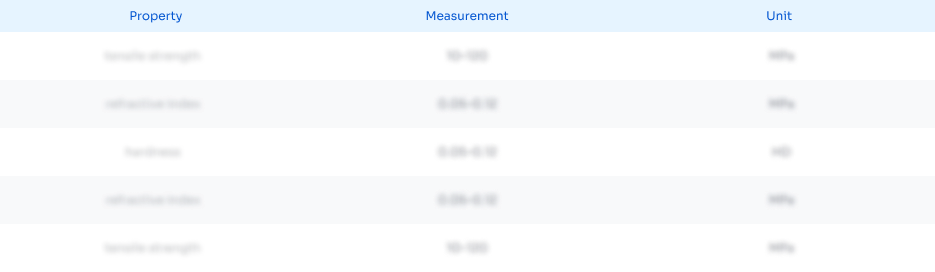
Abstract
Description
Claims
Application Information

- R&D
- Intellectual Property
- Life Sciences
- Materials
- Tech Scout
- Unparalleled Data Quality
- Higher Quality Content
- 60% Fewer Hallucinations
Browse by: Latest US Patents, China's latest patents, Technical Efficacy Thesaurus, Application Domain, Technology Topic, Popular Technical Reports.
© 2025 PatSnap. All rights reserved.Legal|Privacy policy|Modern Slavery Act Transparency Statement|Sitemap|About US| Contact US: help@patsnap.com