Method for smelting ultra-low carbon steel by low oxygen site in whole process
A technology of ultra-low carbon steel and oxygen level, applied in the manufacture of converters, etc., can solve the problems of subcutaneous pinholes, cracked edges, and secondary oxidation expansion of slabs, so as to improve the level of quantity and shape control, and improve the quality of slabs efficiency and ensure castability
- Summary
- Abstract
- Description
- Claims
- Application Information
AI Technical Summary
Problems solved by technology
Method used
Image
Examples
Embodiment Construction
[0030] Any feature disclosed in this specification, unless specifically stated, can be replaced by other alternative features that are equivalent or have similar purposes. Unless expressly stated otherwise, each feature is only one example of a series of equivalent or similar features. The description is only to help the understanding of the present invention, and should not be regarded as a specific limitation on the present invention.
[0031] Each implementation case of the present invention is all carried out according to the following steps:
[0032] 1. Converter process: ①A method to reasonably control the rise of the bottom of the furnace and improve the effect of bottom blowing. Control the rise of the bottom of the furnace to no more than 100mm to ensure the bottom blowing effect of the converter. Dynamically grasp the air supply effect of the bottom blowing, and judge whether the bottom blowing effect meets the requirements through the exposed quantity. ②Optimize ...
PUM
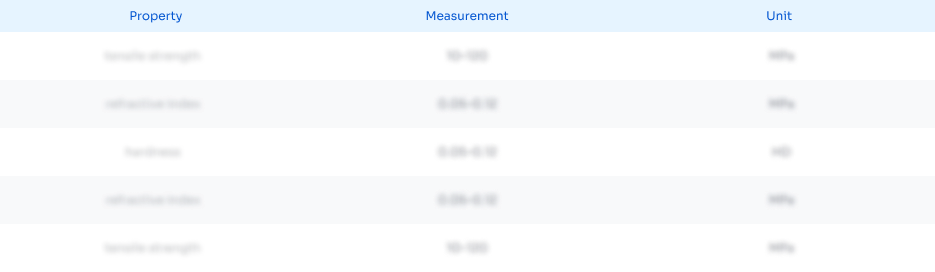
Abstract
Description
Claims
Application Information

- R&D
- Intellectual Property
- Life Sciences
- Materials
- Tech Scout
- Unparalleled Data Quality
- Higher Quality Content
- 60% Fewer Hallucinations
Browse by: Latest US Patents, China's latest patents, Technical Efficacy Thesaurus, Application Domain, Technology Topic, Popular Technical Reports.
© 2025 PatSnap. All rights reserved.Legal|Privacy policy|Modern Slavery Act Transparency Statement|Sitemap|About US| Contact US: help@patsnap.com