Method for judging the melting performance of mold powder
A technology for mold flux and melting performance, which is applied in the investigation stage/state change and other directions, can solve the problems of not taking into account the changing characteristics of the mold flux during the melting process, not being comprehensive enough, and unfavorable for analyzing the surface defects of the casting billet, etc. Achieving great social and economic benefits, ensuring the quality of the casting billet, and high reliability
- Summary
- Abstract
- Description
- Claims
- Application Information
AI Technical Summary
Problems solved by technology
Method used
Image
Examples
Embodiment 1
[0030] The mold flux in Example 1 is a mold flux used for continuous casting of high carbon steel. Sample preparation is carried out according to the method of the present invention, and its melting process and shape characteristics after melting are analyzed. Such as figure 2 Shown is the shape change process of the standard sample of the mold flux of Example 1 of the present invention during the heating process. from figure 2 It can be seen that with the increase of temperature, the shape change characteristic of the standard sample from the softening point to the flow point is uniform, that is, the shape change of the standard sample is stable and uniform, and the entire melting process is uniform. Such as image 3 Shown is the shape of the standard sample after the crystallizer mold flux of Example 1 of the present invention is melted and cooled. from image 3 It can be seen that the standard sample is a uniform circle after melting. According to the shape change c...
Embodiment 2
[0033] The mold flux in Example 2 is a mold flux for slab continuous casting production. Sample preparation is carried out according to the method of the present invention, and its melting process and shape characteristics after melting are analyzed. Such as Figure 4 Shown is the shape change process of the standard sample of the mold flux of Example 2 of the present invention during the heating process. from Figure 4 It can be seen that with the increase of temperature, the shape change of the standard sample from the softening point to the flow point is characterized by undulations, that is, the shape of the standard sample has been fluctuating, and the melting is not uniform throughout the process. Such as Figure 5 Shown is the shape of the standard sample after the crystallizer mold flux of Example 2 of the present invention has been melted and cooled. from Figure 5 It can be seen that the standard sample is uneven and non-circular after melting. According to the...
Embodiment 3
[0036] The mold powder of Example 3 is a mold powder for medium and low carbon continuous casting production. Sample preparation is carried out according to the method of the present invention, and its melting process and shape characteristics after melting are analyzed. As the temperature increases, the shape change of the standard sample from the softening point to the flow point is characterized by a uniform type, that is, the shape change of the standard sample is stable and uniform, and the entire melting process is uniform. The shape change process of the standard sample during the temperature rise process of the mold flux of embodiment 3 can be found in figure 2 . Such as Image 6 Shown is the shape of the standard sample after the crystallizer mold flux of Example 3 of the present invention has been melted and cooled. After melting, the standard sample is uniform and circular. According to the shape change characteristics of the standard sample during the melting ...
PUM
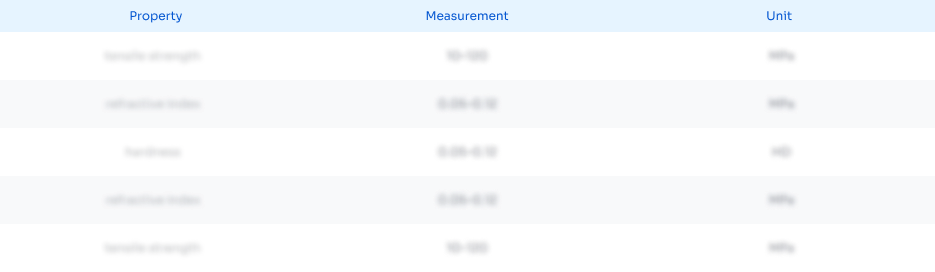
Abstract
Description
Claims
Application Information

- R&D
- Intellectual Property
- Life Sciences
- Materials
- Tech Scout
- Unparalleled Data Quality
- Higher Quality Content
- 60% Fewer Hallucinations
Browse by: Latest US Patents, China's latest patents, Technical Efficacy Thesaurus, Application Domain, Technology Topic, Popular Technical Reports.
© 2025 PatSnap. All rights reserved.Legal|Privacy policy|Modern Slavery Act Transparency Statement|Sitemap|About US| Contact US: help@patsnap.com