Preparation method of aerogel heat-insulation textile composite material
A composite material and airgel technology, applied in textiles and papermaking, conjugated artificial filaments, fiber chemical characteristics, etc., can solve the problems of poor thermal insulation performance and poor durability of thermal insulation and temperature regulating fibers and fabrics, and achieve high porosity , low refractive index, and the effect of narrowing the pore size distribution
- Summary
- Abstract
- Description
- Claims
- Application Information
AI Technical Summary
Problems solved by technology
Method used
Image
Examples
example 1
[0024] Mix ethyl orthosilicate, anhydrous ethanol and deionized water uniformly in a mass ratio of 1:5:8, and stir for 1 h at a stirring speed of 200 r / min to obtain a mixed solution, and adjust the system with a mass fraction of 10% hydrochloric acid solution The pH is 3, continue stirring for 30 minutes to obtain the base solution, drop the ammonia solution into the base solution at a mass ratio of 1:6, and continue stirring for 1 h to obtain a sol; mix the natural fiber and the sol at a mass ratio of 1:3, Stir vigorously at 80°C for 6 hours to obtain spinning dope, and after gel spinning treatment and drawing three times to obtain composite fibers, the composite fibers are soaked in hexamethyldisiloxane for 1 day, and the mass ratio Add trimethylchlorosilane at 1:6, stir evenly, and let it stand for 1 day to obtain modified composite fibers. Gel thermal insulation textile composite material; the gel spinning conditions are: the diameter of the single hole of the spinneret i...
example 2
[0026] Mix ethyl orthosilicate, anhydrous ethanol and deionized water uniformly in a mass ratio of 1:5:8, and stir at a stirring speed of 350 r / min for 1.5 h to obtain a mixed solution, which is adjusted with a mass fraction of 10% hydrochloric acid solution The pH of the system is 3.5, and stirring is continued for 40 min to obtain a base liquid. The ammonia solution is added dropwise to the base liquid at a mass ratio of 1:6, and the stirring is continued for 2 h to obtain a sol; the natural fiber and the sol are mixed at a mass ratio of 1:3, The temperature was 85°C and vigorously stirred for 7 hours to obtain the spinning dope. After gel spinning treatment and stretching for 4 times, the composite fiber was obtained. Add trimethylchlorosilane at a ratio of 1:6, stir evenly, and let it stand for 1 day to obtain modified composite fibers. Gel thermal insulation textile composite material; the gel spinning conditions are: the diameter of the single hole of the spinneret is 0....
example 3
[0028]Mix ethyl orthosilicate, anhydrous ethanol and deionized water uniformly according to the mass ratio of 1:5:8, and stir at a stirring speed of 500 r / min for 2 hours to obtain a mixed solution, and adjust the system with a mass fraction of 10% hydrochloric acid solution The pH is 4, continue stirring for 50min to obtain the base solution, drop the ammonia solution into the base solution at a mass ratio of 1:6, and continue stirring for 3h to obtain a sol; mix the natural fiber and the sol at a mass ratio of 1:3, Stir vigorously at 90 °C for 8 hours to obtain spinning dope, and after gel spinning treatment and stretching for 5 times, composite fibers are obtained. Add trimethylchlorosilane at 1:6, stir evenly, and let it stand for 2 days to obtain modified composite fibers. Gel thermal insulation textile composite material; the gel spinning conditions are: the diameter of the single hole of the spinneret is 1mm, the extrusion speed is 1.4m / min, the spinning temperature is ...
PUM
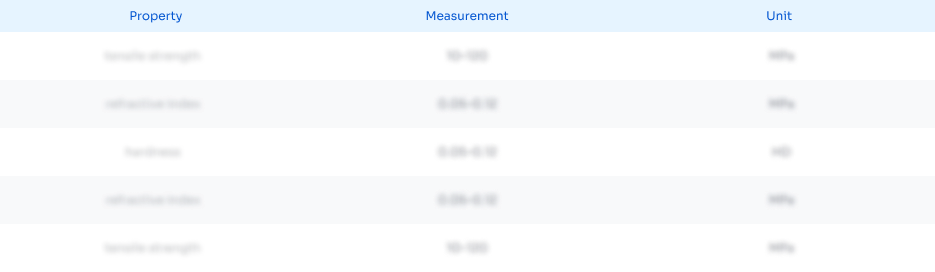
Abstract
Description
Claims
Application Information

- R&D Engineer
- R&D Manager
- IP Professional
- Industry Leading Data Capabilities
- Powerful AI technology
- Patent DNA Extraction
Browse by: Latest US Patents, China's latest patents, Technical Efficacy Thesaurus, Application Domain, Technology Topic, Popular Technical Reports.
© 2024 PatSnap. All rights reserved.Legal|Privacy policy|Modern Slavery Act Transparency Statement|Sitemap|About US| Contact US: help@patsnap.com