Heat treatment method for additive manufacturing monocrystal nickel-base superalloy
A technology of nickel-based superalloy and heat treatment method, applied in the direction of additive processing, etc., can solve the problems of coarse dendrite, slow cooling rate of as-cast superalloy, and reduced degree of component segregation, and achieves simple heat treatment method, optimized alloy performance, The effect of improving the alloy structure
- Summary
- Abstract
- Description
- Claims
- Application Information
AI Technical Summary
Problems solved by technology
Method used
Image
Examples
Embodiment 1
[0038] (a) Put the additively manufactured single crystal nickel-based superalloy to be processed into a heat treatment furnace for solution heat treatment, raise the temperature to 1270° C., take it out after holding it for 0.5 hours, and use air to cool it for the first time, and cool it to room temperature;
[0039] (b) Place the additively manufactured single-crystal nickel-based superalloy after the first cooling into a heat treatment furnace for an aging heat treatment, raise the temperature to 1080° C., and perform a second cooling after holding the temperature for 6 hours, and cool it to room temperature;
[0040] (c) placing the additively manufactured single crystal nickel-based superalloy after the second cooling into a heat treatment furnace for a second aging heat treatment, raising the temperature to 870°C, and cooling for the third time after keeping the temperature for 20 hours, and cooling to room temperature;
[0041] (d) Slicing the processed additively manuf...
Embodiment 2
[0043] (a) Put the additively manufactured single crystal nickel-based superalloy to be processed into a heat treatment furnace for solution heat treatment, raise the temperature to 1280°C, keep it warm for 1.2 hours, use air for the first cooling, and cool to room temperature;
[0044] (b) Place the additively manufactured single-crystal nickel-based superalloy after the first cooling into a heat treatment furnace for an aging heat treatment, raise the temperature to 1070°C, keep it for 8 hours, and then cool it for the second time to room temperature;
[0045] (c) Place the additively manufactured single crystal nickel-based superalloy after the second cooling into a heat treatment furnace for a second aging heat treatment, raise the temperature to 840° C., and perform a third cooling after holding the temperature for 15 hours, and cool to room temperature;
[0046] (d) Slice samples of the additively manufactured single-crystal nickel-based superalloy after heat treatment, a...
Embodiment 3
[0050] (a) Clean up the additively manufactured single crystal nickel-based superalloy to be processed, place it in a heat treatment furnace for solution heat treatment, raise the temperature to 1305° C., keep it warm for 3 hours, use air for the first cooling, and cool to room temperature;
[0051] (b) Place the additively manufactured single-crystal nickel-based superalloy after the first cooling into a heat treatment furnace for an aging heat treatment, raise the temperature to 1080° C., and perform a second cooling after holding the temperature for 6 hours, and cool it to room temperature;
[0052] (c) placing the additively manufactured single crystal nickel-based superalloy after the second cooling into a heat treatment furnace for a second aging heat treatment, raising the temperature to 870°C, and cooling for the third time after keeping the temperature for 20 hours, and cooling to room temperature;
[0053] (d) Slice samples of the treated additively manufactured singl...
PUM
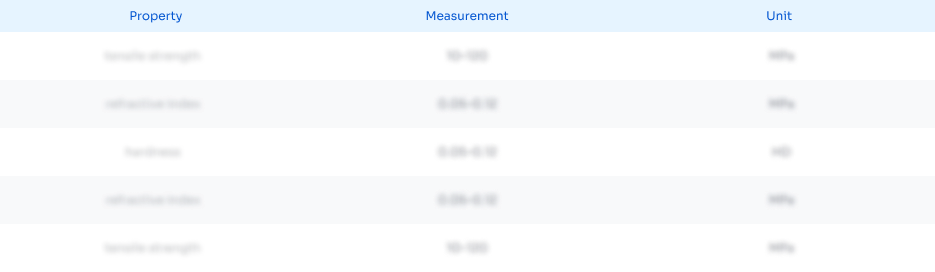
Abstract
Description
Claims
Application Information

- R&D Engineer
- R&D Manager
- IP Professional
- Industry Leading Data Capabilities
- Powerful AI technology
- Patent DNA Extraction
Browse by: Latest US Patents, China's latest patents, Technical Efficacy Thesaurus, Application Domain, Technology Topic, Popular Technical Reports.
© 2024 PatSnap. All rights reserved.Legal|Privacy policy|Modern Slavery Act Transparency Statement|Sitemap|About US| Contact US: help@patsnap.com