Preparation method of plasma assisted super-hydrophobic polyester fabric
A plasma and super-hydrophobic technology, applied in the direction of repelling fibers to liquids, ultrasonic/sonic fiber treatment, fiber types, etc., can solve the problems of difficult processing, great influence on fabric moisture permeability and hand feel, and expensive clothing. , to achieve good mechanical friction stability, easy continuous industrial production, and stable super-hydrophobic performance.
- Summary
- Abstract
- Description
- Claims
- Application Information
AI Technical Summary
Problems solved by technology
Method used
Image
Examples
preparation example Construction
[0021] The invention provides a method for preparing plasma-assisted super-hydrophobic polyester fabric, which combines normal pressure dielectric barrier discharge plasma and a fluorosilane finishing agent to modify the super-hydrophobic properties of polyester fabrics. Atmospheric plasma treatment of polyester fabrics produces a large number of free radicals on the fiber surface, introduces active groups, is energy-saving and environmentally friendly, is easy to operate, and is conducive to continuous production. Fluorosilane finishing agent 1H, 1H, 2H, 2H-perfluorooctyltriethoxysilane is a bifunctional compound that is easy to hydrolyze under acidic conditions to release low-molecular alcohol, and then form active silanol, which can be combined with plasma The hydroxyl group and other oxygen-containing groups on the surface of the treated polyester fiber produce stable chemical bonds, which can give the polyester fabric extremely low surface energy and extremely strong and st...
Embodiment 1
[0035] In this embodiment, the plasma assisted superhydrophobic polyester fabric is prepared according to the following steps:
[0036] Wash and dry the surface of the polyester fabric at a temperature of 90°C. The cleaned polyester fabric is subjected to surface treatment in a dielectric barrier discharge atmospheric pressure plasma device, the plasma treatment atmosphere is Ar gas, the gas flow rate is 1L / min, the treatment power is 1KW, and the treatment time is 120s. The polyester fabric modified by normal pressure plasma is fully padded in the pre-hydrolyzed finishing solution, and the solution is prepared according to the bath ratio of 1:40. The finishing solution includes the following raw materials (by mass): fluorosilane finishing agent 1H, 1 part of 1H, 2H, 2H-perfluorooctyltriethoxysilane, 99 parts of absolute ethanol, 100 parts of deionized water, 1 part of acetic acid, of which fluorosilane is pre-hydrolyzed for 30 minutes. Two dips and two rolls, the padding pressu...
Embodiment 2
[0039] In this embodiment, the plasma assisted superhydrophobic polyester fabric is prepared according to the following steps:
[0040] The surface of the polyester fabric is washed and dried at a temperature of 95°C. The cleaned polyester fabric was subjected to surface treatment in a dielectric barrier discharge atmospheric pressure plasma device, the plasma treatment atmosphere was Ar gas, the gas flow rate was 1L / min, the treatment power was 1KW, and the treatment time was 90s. The polyester fabric modified by normal pressure plasma is fully padded in the pre-hydrolyzed finishing solution, and the solution is prepared according to the bath ratio of 1:40. The finishing solution includes the following raw materials (by mass): fluorosilane finishing agent 1H, 1 part of 1H, 2H, 2H-perfluorooctyl triethoxysilane, 99 parts of absolute ethanol, 100 parts of deionized water, 1 part of acetic acid, pre-hydrolysis of fluorosilane for 30 minutes. Two dips and two rolls, the padding pre...
PUM
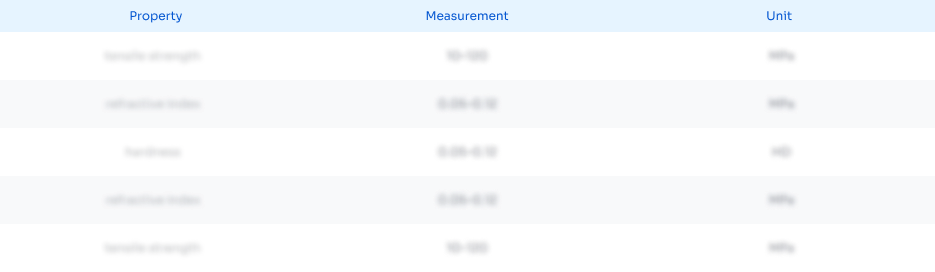
Abstract
Description
Claims
Application Information

- R&D Engineer
- R&D Manager
- IP Professional
- Industry Leading Data Capabilities
- Powerful AI technology
- Patent DNA Extraction
Browse by: Latest US Patents, China's latest patents, Technical Efficacy Thesaurus, Application Domain, Technology Topic, Popular Technical Reports.
© 2024 PatSnap. All rights reserved.Legal|Privacy policy|Modern Slavery Act Transparency Statement|Sitemap|About US| Contact US: help@patsnap.com