Smelting method of low phosphate steel
A smelting method and low-phosphorus steel technology, which are applied in the smelting field of low-phosphorus steel, can solve the problems of low terminal temperature of converter and fluctuation of dephosphorization effect, etc., so as to improve slag effect, reduce splash phenomenon, and promote dephosphorization reaction. Effect
- Summary
- Abstract
- Description
- Claims
- Application Information
AI Technical Summary
Problems solved by technology
Method used
Image
Examples
Embodiment 1
[0040] A 120t top-bottom double-blown converter in a factory adopts this method to smelt cord steel. Using molten iron and scrap steel as raw materials, blowing is carried out in two stages. The first blowing completes desiliconization and dephosphorization, and the second blowing is carried out after the slag is poured. Decarburization, heating, and finally tapping.
[0041]The control parameters of the converter steelmaking process are shown in Table 1. The impact depth of the molten pool h = molten pool depth × impact coefficient, unit cm, the depth of the molten pool is measured by the sub-lance, the impact coefficient is controlled at 0.5-0.7, θ is 12.5°, and the throat diameter D of the oxygen lance nozzle is 3.73cm. When the working oxygen pressure P1 is 0.84MPa, the position H of the oxygen blowing lance is 1.5m; when the working oxygen pressure P1 is 0.69MPa, the position H of the oxygen blowing lance is 1.8m; 1500kg; lift the gun at the end of the first blowing, add...
Embodiment 2
[0046] A 120t top-bottom double-blown converter in a factory adopts this method to smelt cord steel. Using molten iron and scrap steel as raw materials, blowing is carried out in two stages. The first blowing completes desiliconization and dephosphorization, and the second blowing is carried out after the slag is poured. Decarburization, heating, and finally tapping.
[0047] The control parameters of the converter steelmaking process are shown in Table 2. The impact depth of the molten pool h = molten pool depth × impact coefficient, unit cm, the depth of the molten pool is measured by the sub-lance, the impact coefficient is controlled at 0.5-0.7, θ is 12.5°, and the throat diameter D of the oxygen lance nozzle is 3.73cm. When the working oxygen pressure P1 is 0.84MPa, the position H of the oxygen blowing lance is 1.45m; when the working oxygen pressure P1 is 0.69MPa, the position H of the oxygen blowing lance is 1.75m; lime is added at one time for a blowing, and the additi...
PUM
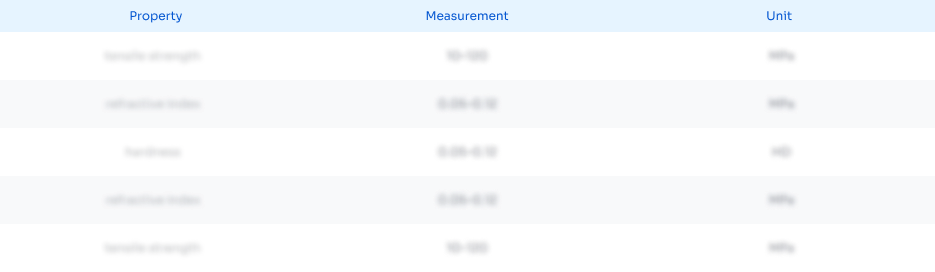
Abstract
Description
Claims
Application Information

- R&D Engineer
- R&D Manager
- IP Professional
- Industry Leading Data Capabilities
- Powerful AI technology
- Patent DNA Extraction
Browse by: Latest US Patents, China's latest patents, Technical Efficacy Thesaurus, Application Domain, Technology Topic, Popular Technical Reports.
© 2024 PatSnap. All rights reserved.Legal|Privacy policy|Modern Slavery Act Transparency Statement|Sitemap|About US| Contact US: help@patsnap.com