Application of ladle bottom low-nickel-chromium residual iron in plain carbon steel smelting process
A common carbon steel, nickel-chromium technology, applied to the application field of low-nickel-chromium residual iron in the smelting process of common carbon steel, which can solve the problems of unsatisfactory effects, weakened carbon-oxygen reaction, and reduced oxygen supply intensity. , to achieve uniform and stable oxidation reaction, reduce splashing, and reduce the amount of use
- Summary
- Abstract
- Description
- Claims
- Application Information
AI Technical Summary
Problems solved by technology
Method used
Image
Examples
Embodiment 1
[0012] An application of low-nickel-chromium-iron residual iron at the bottom of the ordinary carbon steel smelting process, which includes using a low-nickel-chromium iron ladle with solidification of low-nickel-chromium iron water waste liquid at the bottom of the ladle in the early smelting process of the converter top blowing steelmaking process Connect high-temperature ordinary carbon molten iron so that low-nickel-chromium residual iron is melted in high-temperature molten iron to obtain mixed molten iron, and then the mixed molten iron is blended into the converter and blown together with ordinary carbon scrap steel. The content is 0.15%.
Embodiment 2-6
[0014] Examples 2-6 adopt the same scheme as Example 1, the difference lies in the content of chromium in the mixed molten iron is different.
PUM
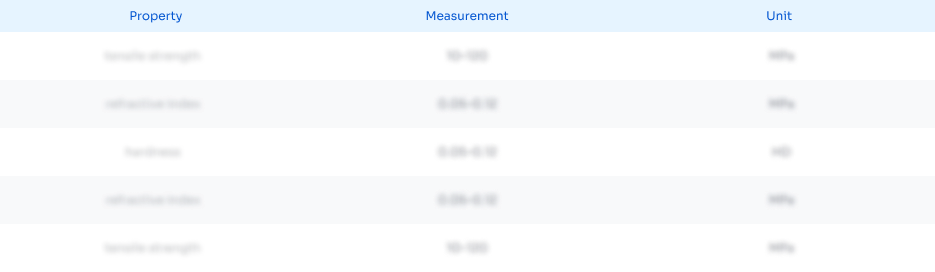
Abstract
Description
Claims
Application Information

- R&D Engineer
- R&D Manager
- IP Professional
- Industry Leading Data Capabilities
- Powerful AI technology
- Patent DNA Extraction
Browse by: Latest US Patents, China's latest patents, Technical Efficacy Thesaurus, Application Domain, Technology Topic, Popular Technical Reports.
© 2024 PatSnap. All rights reserved.Legal|Privacy policy|Modern Slavery Act Transparency Statement|Sitemap|About US| Contact US: help@patsnap.com