Ferronickel compound oxide catalyst and preparation method and application thereof
A composite oxide and catalyst technology, applied in metal/metal oxide/metal hydroxide catalysts, physical/chemical process catalysts, chemical instruments and methods, etc., to achieve strong water and sulfur resistance, high N2 selectivity, The effect of promoting dispersion
- Summary
- Abstract
- Description
- Claims
- Application Information
AI Technical Summary
Problems solved by technology
Method used
Image
Examples
Embodiment 1
[0030] (1) Weigh 0.19 g of nickel nitrate hexahydrate, 0.13 g of ferric nitrate nonahydrate, 0.045 g of urea, and 0.005 g of sodium citrate, dissolve them in 40ml of distilled water, and stir with a magnetic stirrer for 10 minutes to completely dissolve until the solution is clear.
[0031] (2) The mixed solution obtained in (1) was sealed and placed in a polytetrafluoroethylene-lined stainless steel reactor, and hydrothermally treated in an oven at 120 °C for 12 h, and the pH value of the solution was 7.6.
[0032] (3) After the reaction kettle is naturally cooled, filter the reacted solution to get the precipitate, wash it with deionized water several times until neutral, put it in an oven and dry it at 80 °C for 12 h, take it out and grind it Sieve to obtain the NiFe-LDH precursor.
[0033] (4) Put the NiFe-LDH precursor in the crucible, put it into the muffle furnace, set the heating process (heating rate 2 ℃ / min) from room temperature to 400 ℃, calcined at 400 ℃ for 3 hou...
Embodiment 2
[0039] (1) Weigh 0.23 g of nickel nitrate hexahydrate, 0.081 g of ferric nitrate nonahydrate, 0.043 g of urea, and 0.003 g of sodium citrate, dissolve them in 40ml of distilled water, and stir with a magnetic stirrer for 10 minutes to completely dissolve until the solution is clear.
[0040] (2) The mixed solution obtained in (1) was sealed and placed in a polytetrafluoroethylene-lined stainless steel reactor, and hydrothermally treated in an oven at 120 °C for 12 h, and the pH of the solution was 7.3.
[0041] (3) After the reaction kettle is naturally cooled, filter the reacted solution to get the precipitate, wash it with deionized water several times until it becomes neutral, put it in an oven and dry it for 12 hours at 80 °C, take it out and grind it to sieve , namely the NiFe-LDH precursor.
[0042] (4) Put the NiFe-LDH precursor in the crucible, put it into the muffle furnace, set the heating process (heating rate is 2°C / min) from room temperature to 500°C, and calcinat...
Embodiment 3
[0049] (1) Weigh 0.25 g of nickel nitrate hexahydrate, 0.058 g of ferric nitrate nonahydrate, 0.042 g of urea, and 0.002 g of sodium citrate, dissolve them in 40 ml of distilled water, and stir with a magnetic stirrer for 10 minutes to completely dissolve until the solution is clear.
[0050] (2) The mixed solution obtained in (1) was sealed and placed in a polytetrafluoroethylene-lined stainless steel reactor, and hydrothermally treated in an oven at 120 °C for 12 h, and the pH of the solution was 6.8.
[0051] (3) After the reaction kettle is naturally cooled, filter the reacted solution to get the precipitate, wash it with deionized water several times until it becomes neutral, put it in an oven and dry it for 12 hours at 80 °C, take it out and grind it to sieve , namely the NiFe-LDH precursor.
[0052] (4) Put the NiFe-LDH precursor in the crucible, put it into the muffle furnace, set the heating process (heating rate is 2°C / min) from room temperature to 600°C, and calcina...
PUM
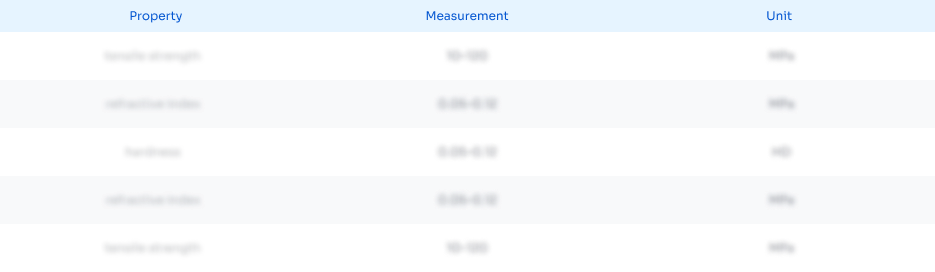
Abstract
Description
Claims
Application Information

- R&D
- Intellectual Property
- Life Sciences
- Materials
- Tech Scout
- Unparalleled Data Quality
- Higher Quality Content
- 60% Fewer Hallucinations
Browse by: Latest US Patents, China's latest patents, Technical Efficacy Thesaurus, Application Domain, Technology Topic, Popular Technical Reports.
© 2025 PatSnap. All rights reserved.Legal|Privacy policy|Modern Slavery Act Transparency Statement|Sitemap|About US| Contact US: help@patsnap.com