Preparation method of high-bonding type copper-based electrical contact material
A technology of electrical contact materials and bonding, which is applied in the direction of conductive materials dispersed in non-conductive inorganic materials, cable/conductor manufacturing, circuits, etc., can solve the problems of poor performance of electrical contact materials and low bonding strength, and achieve improved bonding properties, improving structural characteristics, improving the effect of mechanical strength and mechanical properties
- Summary
- Abstract
- Description
- Claims
- Application Information
AI Technical Summary
Problems solved by technology
Method used
Image
Examples
example 1
[0018] In parts by weight, weigh 90 parts of deionized water, 3 parts of peach gum, 1 part of silver nitrate and 3 parts of trisodium citrate in a beaker, stir and mix them and place them under ultraviolet light for 3 hours, stir and mix And collect the mixed sol solution; then weigh 45 parts of deionized water, 2 parts of aluminum nitrate, and 3 parts of lactic acid respectively in a beaker according to parts by weight, mix and place at room temperature to stir and react for 6 hours, collect the mixed solution and place In a rotary evaporator, evaporate at 75°C to 1 / 5 of the original volume, collect the rotary sol and mix it with a volume ratio of 1:1, stir and mix the mixed sol and the rotary sol and place it under 200W for ultrasonic dispersion 10min, collect the dispersion sol; by weight, weigh 45 parts of copper powder, 10 parts of dispersion sol and 1 part of lanthanum respectively and place them in a ball mill tank, collect the ball mill slurry after ball milling at room...
example 2
[0020] In parts by weight, weigh 95 parts of deionized water, 4 parts of peach gum, 2 parts of silver nitrate and 4 parts of trisodium citrate in a beaker, stir and mix them and place them under ultraviolet light for 2 hours, stir and mix And collect the mixed sol solution; then weigh 47 parts of deionized water, 2 parts of aluminum nitrate, and 4 parts of lactic acid in a beaker according to parts by weight, mix and place it at room temperature for stirring and reacting for 7 hours, collect the mixed solution and place In a rotary evaporator, evaporate at 80°C to 1 / 5 of the original volume, collect the rotary sol and mix it with a volume ratio of 1:1, stir and mix the mixed sol and the rotary sol and place it under 250W for ultrasonic dispersion 12min, collect the dispersion sol; weigh 47 parts of copper powder, 12 parts of dispersion sol and 2 parts of lanthanum respectively in the ball mill tank, collect the ball mill slurry after ball milling at room temperature for 4 hours...
example 3
[0022] In parts by weight, weigh 100 parts of deionized water, 5 parts of peach gum, 2 parts of silver nitrate and 5 parts of trisodium citrate in a beaker, stir and mix them and place them under ultraviolet light for 5 hours, stir and mix And collect the mixed sol solution; then weigh 50 parts of deionized water, 3 parts of aluminum nitrate, and 5 parts of lactic acid in a beaker, mix them and place them at room temperature for 8 hours, collect the mixed solution and place In a rotary evaporator, evaporate at 85°C to 1 / 5 of the original volume, collect the rotary sol and mix it with a volume ratio of 1:1, stir and mix the mixed sol and the rotary sol and place it under 300W for ultrasonic dispersion 15min, collect the dispersed sol; weigh 50 parts of copper powder, 15 parts of dispersed sol and 2 parts of lanthanum respectively in the ball mill tank, collect the ball mill slurry after ball milling at room temperature for 5 hours, and pour the ball mill slurry Put the mold int...
PUM
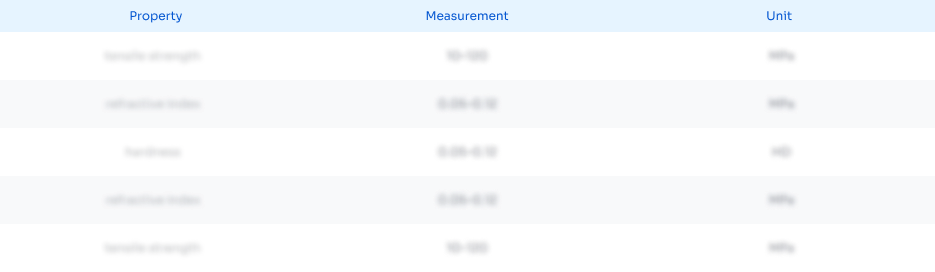
Abstract
Description
Claims
Application Information

- R&D Engineer
- R&D Manager
- IP Professional
- Industry Leading Data Capabilities
- Powerful AI technology
- Patent DNA Extraction
Browse by: Latest US Patents, China's latest patents, Technical Efficacy Thesaurus, Application Domain, Technology Topic, Popular Technical Reports.
© 2024 PatSnap. All rights reserved.Legal|Privacy policy|Modern Slavery Act Transparency Statement|Sitemap|About US| Contact US: help@patsnap.com