Ferromagnetic Alloy Vacuum Melting Casting Short Process Precision Casting Method
A precision casting and ferromagnetic technology, applied in the direction of casting molding equipment, etc., can solve the problems of inability to solve the problems of alloy smelting oxidation burning and gas absorption, the temperature loss of pouring and filling liquid alloys, and the inability to effectively improve the metallurgical quality of castings, etc., to achieve Avoid shell cracking and liquid alloy temperature loss, avoid pouring liquid alloy temperature loss, and improve the quality of castings
- Summary
- Abstract
- Description
- Claims
- Application Information
AI Technical Summary
Problems solved by technology
Method used
Image
Examples
Embodiment 1
[0031] Utilize the ferromagnetic alloy vacuum melting and casting short flow precision casting method of the present invention, trial-manufacture the turbine impeller of automobile turbocharger, for example J130B turbine impeller, comprise the following steps:
[0032] Step 1. Determine the casting process plan according to the shape and structure of the impeller. Three pieces of one type are uniformly distributed at 120° on the same horizontal plane. The pattern material is polypropylene, and the pattern forming processing mold is designed and manufactured.
[0033] Step 2, using polystyrene to manufacture the cylindrical charging cavity pattern, the casting molding injection port pattern and the impeller casting pattern by the injection molding method, and the charging cavity pattern and the injection port pattern are integrated injection molding.
[0034]Step 3, assembling the shape of the cylindrical charging cavity, the shape of the casting injection port and the shape of ...
Embodiment 2
[0041] The production of automobile turbocharger turbine impeller J130B by investment casting in the traditional way includes the following steps:
[0042] Step 1. Determine the casting process plan according to the shape and structure of the impeller. Three pieces of one type are evenly distributed at 120° on the same horizontal plane. Design the pouring system. The wax mold is made of medium-temperature wax, and the wax mold molding mold is designed and manufactured.
[0043] Step 2, making sprue cup, sprue, inner sprue and casting wax mold with medium temperature wax.
[0044] Step 3, according to the design requirements of the casting process, the sprue cup, the sprue, the inner runner and the casting pattern of the impeller are welded into an integral wax mold group and trimmed.
[0045] Step 3: Dip-coat the surface layer slurry, shake the slurry, sprinkle surface sand, and dry for 26 to 28 hours to make the surface layer; after the surface layer is dried, dip-coat the ba...
Embodiment 3
[0051] Utilize the ferromagnetic alloy vacuum melting and casting short flow precision casting method of the present invention, trial-manufacture the turbine impeller of automobile turbocharger, for example K418superalloy SJ50 turbine impeller, comprise the following steps:
[0052] Step 1. Determine the casting process plan according to the shape and structure of the impeller. There are 6 pieces in the first type, which are distributed in two different horizontal positions. The 3 pieces in each horizontal position are evenly distributed at 120°, and the castings in the two different horizontal positions are arranged in a 60° cross arrangement. , The shape material is made of polyethylene, and the shape forming processing mold is designed and manufactured.
[0053] Step 2, using polyethylene to manufacture a cylindrical charging cavity pattern, a casting molding injection port pattern and an impeller casting pattern by injection molding, the charging cavity pattern and the inje...
PUM
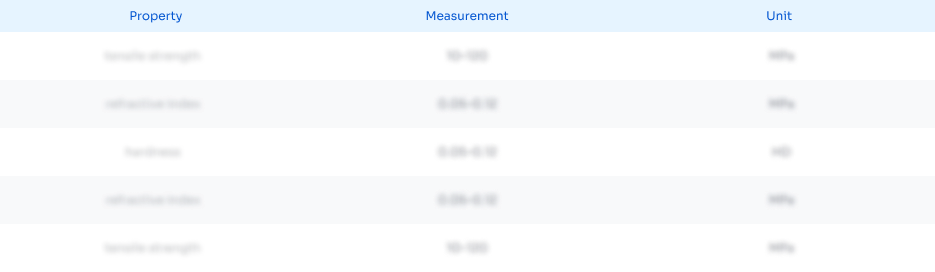
Abstract
Description
Claims
Application Information

- R&D
- Intellectual Property
- Life Sciences
- Materials
- Tech Scout
- Unparalleled Data Quality
- Higher Quality Content
- 60% Fewer Hallucinations
Browse by: Latest US Patents, China's latest patents, Technical Efficacy Thesaurus, Application Domain, Technology Topic, Popular Technical Reports.
© 2025 PatSnap. All rights reserved.Legal|Privacy policy|Modern Slavery Act Transparency Statement|Sitemap|About US| Contact US: help@patsnap.com