Preparation method of high-performance water-soluble high-solid low-viscosity acrylic resin
A kind of acrylic resin, water-soluble technology, applied in paints containing biocide, anti-fouling/underwater coatings, coatings, etc., can solve the problem of poor flexibility and heat and humidity resistance of water-based acrylic resin coatings, and cannot meet the high-performance coating requirements and other problems, to achieve the effect of strong impact resistance, moderate molecular weight and high reactivity
- Summary
- Abstract
- Description
- Claims
- Application Information
AI Technical Summary
Problems solved by technology
Method used
Image
Examples
preparation example Construction
[0040] The present invention relates to a preparation method and application of a high-performance water-soluble high-solid and low-viscosity acrylic resin. The material formula used in the preparation method of the acrylic resin in this example is as follows: 7-12 parts of acrylic acid, 10-25 parts of n-butyl acrylate , 0-10 parts of n-butyl methacrylate, 10-20 parts of styrene, 10-30 parts of methyl methacrylate, 1-6 parts of laurate methacrylate, 2-10 parts of vinyl tertiary carbonate, methyl 26-35 parts of hydroxyethyl acrylate, 1-6 parts of methacryloxypropyl trimethoxysilane, 0.75-2.25 parts of chain transfer agent, 1.8-6.7 parts of initiator, 4.4-12 parts of amine neutralizer .
[0041] The steps of the preparation method of present embodiment acrylic resin are as follows:
[0042] (1) Prepare dry and clean reaction kettles and dripping kettles to ensure smooth pipelines, normal operation of instruments, valves, and motors, and normal use of steam, water cooling, stirr...
Embodiment 1
[0062] Take 40 parts of n-butanol and 23 parts of isopropanol into the reaction kettle, stir to fill with nitrogen, heat to reflux, and control the reaction temperature at 82±2°C; add 9 parts of acrylic acid, 10 parts of n-butyl acrylate, and 2 parts of vinyl tert-carbonate , 2 parts of laurate methacrylate, 15 parts of styrene, 28.5 parts of methyl methacrylate, 32.5 parts of hydroxyethyl methacrylate, 1.8 parts of dodecyl mercaptan, 3.6 parts of azobisisobutyronitrile Stir in the dripping kettle, fully mix and dissolve; 3.5 hours to complete the dripping; keep warm for 15 minutes, add 1 part of methacryloxypropyl trimethoxysilane and 2 parts of isopropanol into the dropping kettle and stir, and finish dripping for 15 minutes; continue to keep warm 1h, add 0.4 parts of azobisisobutyronitrile and 2 parts of ethanol into the dripping kettle and stir, fully mix and dissolve; after 0.5h of dripping, keep warm for 1h; Add 5.6 parts of N,N-dimethylethanolamine into the dripping ket...
Embodiment 2
[0064] Take 40 parts of propylene glycol methyl ether and 23 parts of ethylene glycol butyl ether into the reactor, stir to fill with nitrogen, heat to reflux, and control the reaction temperature at 91±2°C; add 9 parts of acrylic acid, 12 parts of n-butyl acrylate, vinyl tertiary 6 parts, 1 part of laurate methacrylate, 15 parts of styrene, 23.5 parts of methyl methacrylate, 32.5 parts of hydroxyethyl methacrylate, 1.25 parts of lauryl mercaptan, 1.8 parts of benzoyl peroxide Add to the dripping kettle and stir, fully mix and dissolve; 3.5 hours to complete the dripping; keep warm for 15 minutes, add 1 part of methacryloxypropyltrimethoxysilane and 2 parts of isopropanol to the dropping kettle and stir, and the dripping is completed for 15 minutes; continue Keep warm for 1h, add 0.2 parts of benzoyl peroxide, 1 part of ethyl acetate, and 1 part of isopropanol into the dripping kettle and stir, fully mix and dissolve; after 0.5h of dripping, keep warm for 1h; stop heating, pass...
PUM
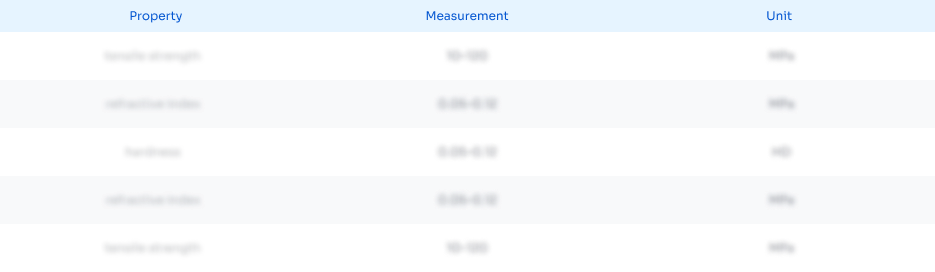
Abstract
Description
Claims
Application Information

- R&D
- Intellectual Property
- Life Sciences
- Materials
- Tech Scout
- Unparalleled Data Quality
- Higher Quality Content
- 60% Fewer Hallucinations
Browse by: Latest US Patents, China's latest patents, Technical Efficacy Thesaurus, Application Domain, Technology Topic, Popular Technical Reports.
© 2025 PatSnap. All rights reserved.Legal|Privacy policy|Modern Slavery Act Transparency Statement|Sitemap|About US| Contact US: help@patsnap.com