Protective atmosphere short-period roll bottom type continuous annealing furnace production line
A continuous annealing furnace and protective atmosphere technology, applied in furnaces, furnace types, heat treatment furnaces, etc., can solve problems such as affecting production efficiency, easy entry of oxygen into the furnace body, process interference, etc., to achieve automation, intelligence, and convenience. Programmatic management, the effect of expanding the scope of application
- Summary
- Abstract
- Description
- Claims
- Application Information
AI Technical Summary
Problems solved by technology
Method used
Image
Examples
Embodiment Construction
[0047] refer to Figure 1 to Figure 10 A protective atmosphere short cycle roller hearth continuous annealing furnace production line is shown, including a feeding table 1, a feeding vacuum chamber 2, a preheating chamber 3, a heating chamber 4, an isothermal chamber 5, a slow cooling chamber 6, and a discharge vacuum chamber Chamber 7 and discharge table 8, described feeding table 1, feed vacuum chamber 2, preheating chamber 3, heating chamber 4, etc. greenhouse 5, slow cooling chamber 6, discharge vacuum chamber 7 and discharge table 8 The interior is equipped with idler rollers 45, and the feeding platform 1, feeding vacuum chamber 2, preheating chamber 3, heating chamber 4, isothermal chamber 5, slow cooling chamber 6, discharging vacuum chamber 7 and discharging platform 8 are all It is connected with a computer and automatically controlled by a PLC program. The bottom of the feeding table 1 is provided with a feeding table transmission motor 9. The feeding table transmis...
PUM
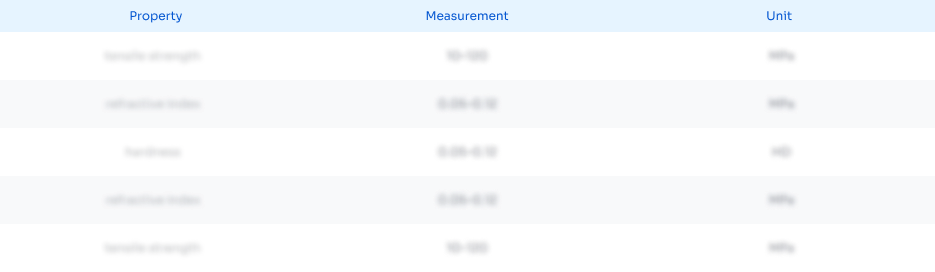
Abstract
Description
Claims
Application Information

- R&D
- Intellectual Property
- Life Sciences
- Materials
- Tech Scout
- Unparalleled Data Quality
- Higher Quality Content
- 60% Fewer Hallucinations
Browse by: Latest US Patents, China's latest patents, Technical Efficacy Thesaurus, Application Domain, Technology Topic, Popular Technical Reports.
© 2025 PatSnap. All rights reserved.Legal|Privacy policy|Modern Slavery Act Transparency Statement|Sitemap|About US| Contact US: help@patsnap.com