Method of making paper by machinery
A machine manufacturing and paper technology, applied in paper, papermaking, textiles and papermaking, etc., can solve the problems of reducing pulp whiteness, inability to effectively remove metal ions, and limit material selection, etc., to achieve the effect of increasing the degree of yellowing
- Summary
- Abstract
- Description
- Claims
- Application Information
AI Technical Summary
Problems solved by technology
Method used
Examples
Embodiment 1
[0045] A method for machine-made paper in this embodiment includes a pulping process, a modulation process, a papermaking process, and a post-processing process. The pulping process is divided into two steps: plant fiber raw material pulping and bleaching. The modulation process is divided into two steps: For the three steps of loose pulp, beating and sizing and filling, in this embodiment, other processes adopt a method similar to that of existing machine-made paper, the difference is:
[0046] After the plant fiber raw material pulping step and before the bleaching step, component A was added, stirred at a stirring speed of 170 r / min at a temperature of 34°C for 7 minutes, and then left to stand for 30 minutes to proceed to the next step;
[0047]Add component B before the sizing step in the preparation process, stir at a stirring speed of 10r / min for 50 minutes at a temperature of 28°C and transfer to the next step;
[0048] The component A includes the following raw materi...
Embodiment 2
[0064] A method for machine-made paper in this embodiment includes a pulping process, a modulation process, a papermaking process, and a post-processing process. The pulping process is divided into two steps: plant fiber raw material pulping and bleaching. The modulation process is divided into two steps: For the three steps of loose pulp, beating and sizing and filling, in this embodiment, other processes adopt a method similar to that of existing machine-made paper, the difference is:
[0065] Add component A after the plant fiber raw material pulping step and before the bleaching step, stir at a temperature of 36°C at a stirring speed of 180r / min for 9 minutes, then let stand for 34 minutes and transfer to the next step;
[0066] Add component B before the sizing step in the preparation process, stir for 70 minutes at a stirring speed of 14r / min at a temperature of 30°C and transfer to the next step;
[0067] The component A includes the following raw materials in parts by ...
Embodiment 3
[0083] A method for machine-made paper in this embodiment includes a pulping process, a modulation process, a papermaking process, and a post-processing process. The pulping process is divided into two steps: plant fiber raw material pulping and bleaching. The modulation process is divided into two steps: For the three steps of loose pulp, beating and sizing and filling, in this embodiment, other processes adopt a method similar to that of existing machine-made paper, the difference is:
[0084] After the plant fiber raw material pulping step and before the bleaching step, component A was added, stirred at a stirring speed of 175 r / min for 8 minutes at a temperature of 35° C., and then left to stand for 32 minutes and transferred to the next step;
[0085] Add component B before the sizing step in the preparation process, and stir for 60 minutes at a stirring speed of 12r / min at a temperature of 29°C and transfer to the next step;
[0086] The component A includes the followin...
PUM
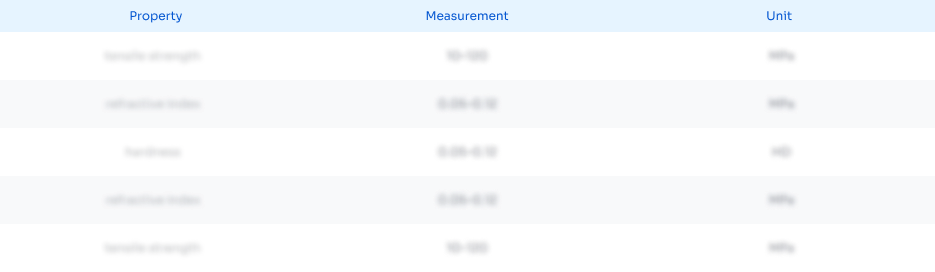
Abstract
Description
Claims
Application Information

- Generate Ideas
- Intellectual Property
- Life Sciences
- Materials
- Tech Scout
- Unparalleled Data Quality
- Higher Quality Content
- 60% Fewer Hallucinations
Browse by: Latest US Patents, China's latest patents, Technical Efficacy Thesaurus, Application Domain, Technology Topic, Popular Technical Reports.
© 2025 PatSnap. All rights reserved.Legal|Privacy policy|Modern Slavery Act Transparency Statement|Sitemap|About US| Contact US: help@patsnap.com