Preparation method and powder feeding device of ceramic powder reinforced metal base welding layer
A technology of ceramic powder and powder feeding device, which is applied in metal processing equipment, welding equipment, plasma welding equipment and other directions, can solve the problems of low utilization rate of powder, serious powder burning loss, and enhance the applicability of external powder feeding device, etc. The effect of avoiding serious burning loss, alleviating powder sinking, and good surfacing effect
- Summary
- Abstract
- Description
- Claims
- Application Information
AI Technical Summary
Problems solved by technology
Method used
Image
Examples
preparation example Construction
[0034] refer to figure 1 with figure 2 , a preparation method of ceramic powder reinforced metal-based welding layer, comprising the following steps:
[0035] Step S10, pretreating the metal matrix, alloy powder and ceramic powder;
[0036] Step S20, setting the plasma surfacing process parameters according to the metal base material, and determining the powder feeding temperature of the powder feeding device according to the properties of the alloy powder;
[0037]Step S30, place the pre-processed metal substrate on the workbench, turn on the plasma surfacing machine and the powder feeding device, and control the powder feeding device to move automatically, the temperature sensing device of the powder feeding device detects the temperature distribution of the molten metal pool and transmits the temperature field The control device 8 of the powder feeding device (computer can be used), the control device 8 matches the current temperature field data with the preset powder fe...
Embodiment 1
[0049] The metal matrix material is selected as hot work die steel 4Cr5MoSiV1, also known as H13 steel. H13 steel has a large hardening tendency, and it is directly surfacing on its surface, and the weld layer is prone to cracks. Therefore, it is necessary to pre-treat H13 steel before welding. Put H13 steel in a holding furnace to preheat to 300°C and keep it warm for half an hour. Then use a grinder to quickly polish the surface of the substrate to remove the oxide scale on the surface. The powder used in the experiment is Ni60A nickel-based self-fluxing alloy powder and WC ceramic powder. Put the powder into the external powder feeding container, cover the sealing cover, check whether the powder feeding of the welding machine is normal, and whether there is any powder blocking the pipeline. If the powder feeding works normally, put the processed H13 steel into the working table. Turn on the computer, plasma gas, shielding gas, and powder gas, start the welding machine, and...
Embodiment 2
[0051] Choose H13 steel for the metal matrix, choose Ni60A for the alloy powder, and choose Cr for the ceramic powder 3 C 2 . Clean and preheat the surface of the H13 steel substrate, dry and cool the powder, put Ni60A into the synchronous powder feeder, Cr 3 C 2 Load the external powder feeder. The powder feeding temperature of the powder feeding device is set at 2000°C, the welding current is 80A, the synchronous powder feeding speed is 10g / min, the welding torch forward speed is 50mm / min, the swing amplitude is 12mm, the swing frequency is 50c / min, and the nozzle distance is 9mm. The powder feeding speed is 6g / min. The front and rear swings of the external powder delivery pipe 2 are 3°, and the swing speed is 12° / S. Cr 3 C 2 The melting point of the powder is low, and it is easy to be burned when the temperature is too high, so the external powder feeding swing and swing speed can be appropriately reduced, and the powder feeding range can be reduced.
[0052] figu...
PUM
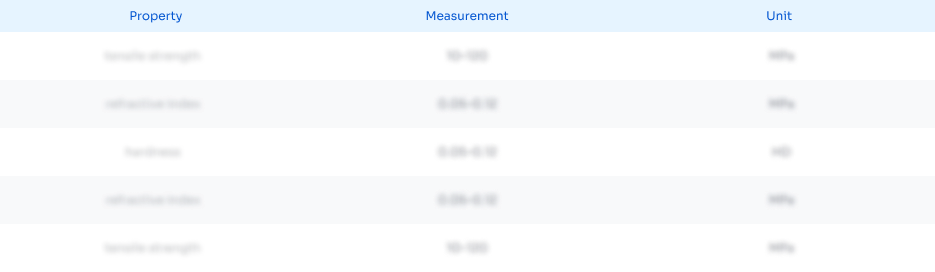
Abstract
Description
Claims
Application Information

- Generate Ideas
- Intellectual Property
- Life Sciences
- Materials
- Tech Scout
- Unparalleled Data Quality
- Higher Quality Content
- 60% Fewer Hallucinations
Browse by: Latest US Patents, China's latest patents, Technical Efficacy Thesaurus, Application Domain, Technology Topic, Popular Technical Reports.
© 2025 PatSnap. All rights reserved.Legal|Privacy policy|Modern Slavery Act Transparency Statement|Sitemap|About US| Contact US: help@patsnap.com