High-efficiency infrared micro Fresnel lens array manufacturing method based on MEMS technology
A lens array and manufacturing method technology, applied in the field of sensors, can solve the problems of silicon-based or germanium-based mass production, low infrared transmittance of lens array resin lenses, etc., to reduce process costs and production time, improve imaging efficiency, Efficient and easy-to-control process
- Summary
- Abstract
- Description
- Claims
- Application Information
AI Technical Summary
Problems solved by technology
Method used
Image
Examples
Embodiment Construction
[0034] Such as Figure 6-Figure 10 A method for manufacturing an efficient infrared micro-Fresnel lens array based on MEMS technology, which includes the following MEMS process steps,
[0035] a, using the Fresnel diffraction principle to form a diffraction image;
[0036] b. The steps of making the diffraction screen: such as Figure 6 , Figure 7 As shown, several light-transmitting small hole array patterns are set on the photolithography plate or metal plate 2, and the radius of the small hole 1 is L 0 And it is arranged on the upper surface of the light-transmitting quartz plate 3 to form a diffraction screen, and the metal plate can be a chromium metal plate;
[0037] c. The step of making the receiving screen: coating a positive photosensitive photoresist 4 on the surface of the silicon wafer as the substrate 5 to form a receiving screen, and the distance between the receiving screen and the diffraction screen is z;
[0038] d, the step of exposure forming photoresi...
PUM
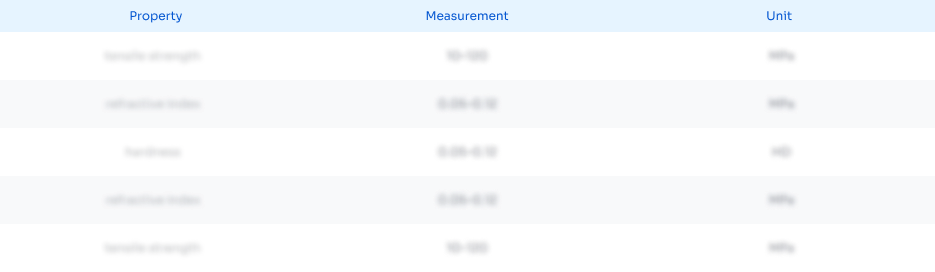
Abstract
Description
Claims
Application Information

- R&D
- Intellectual Property
- Life Sciences
- Materials
- Tech Scout
- Unparalleled Data Quality
- Higher Quality Content
- 60% Fewer Hallucinations
Browse by: Latest US Patents, China's latest patents, Technical Efficacy Thesaurus, Application Domain, Technology Topic, Popular Technical Reports.
© 2025 PatSnap. All rights reserved.Legal|Privacy policy|Modern Slavery Act Transparency Statement|Sitemap|About US| Contact US: help@patsnap.com