Wear-resistant material
A technology of wear-resistant materials and raw materials, applied in the field of wear-resistant materials, can solve the problems of premature bearing failure, decrease in hardness of bearing materials, re-dissolution, etc., and achieve the effect of excellent high temperature resistance and wear resistance.
- Summary
- Abstract
- Description
- Claims
- Application Information
AI Technical Summary
Problems solved by technology
Method used
Examples
Embodiment 1
[0010] Embodiment 1: A wear-resistant material is composed of the following raw materials in parts by weight: 15-30 parts of tungsten metal powder, 30-50 parts of titanium carbide, 15-25 parts of copper metal powder, 40-50 parts of silicon carbide grains 20-25 parts of flake corundum, 15-20 parts of molybdenum disulfide, 5-8 parts of magnesium oxide, 2-5 parts of nickel fluoride, 3-5 parts of niobium, and 0.5-5 parts of toughening agent.
Embodiment 2
[0011] Embodiment 2: A wear-resistant material is composed of the following raw materials in parts by weight: 15 parts of tungsten metal powder, 30 parts of titanium carbide, 15 parts of copper metal powder, 40 parts of silicon carbide grains, 20 parts of flaky corundum, 15 parts of molybdenum disulfide, 5 parts of magnesium oxide, 2 parts of nickel fluoride, 3 parts of niobium, and 0.5 parts of toughening agent.
Embodiment 3
[0012] Embodiment 3: A wear-resistant material is composed of the following raw materials in parts by weight: 30 parts of tungsten metal powder, 50 parts of titanium carbide, 25 parts of copper metal powder, 50 parts of silicon carbide grains, 25 parts of flaky corundum, 20 parts of molybdenum disulfide, 8 parts of magnesium oxide, 5 parts of nickel fluoride, 5 parts of niobium, and 5 parts of toughening agent.
PUM
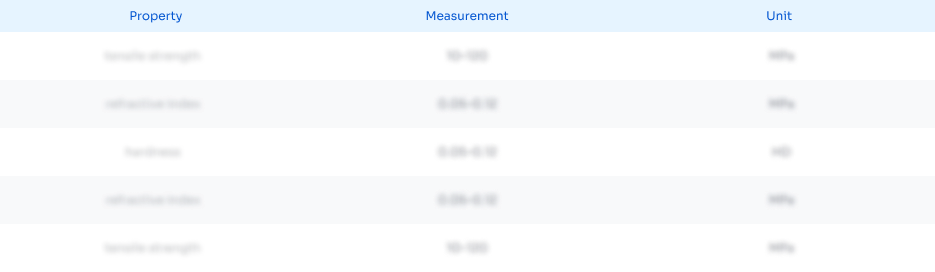
Abstract
Description
Claims
Application Information

- R&D Engineer
- R&D Manager
- IP Professional
- Industry Leading Data Capabilities
- Powerful AI technology
- Patent DNA Extraction
Browse by: Latest US Patents, China's latest patents, Technical Efficacy Thesaurus, Application Domain, Technology Topic, Popular Technical Reports.
© 2024 PatSnap. All rights reserved.Legal|Privacy policy|Modern Slavery Act Transparency Statement|Sitemap|About US| Contact US: help@patsnap.com