An electric propulsion deployment and thrust direction adjustment mechanism
An adjustment mechanism and electric propulsion technology, applied in the direction of space vehicle propulsion system devices, space vehicle guidance devices, etc., can solve the problems that electric thrusters cannot form a complete backup, low efficiency, and reduce the effective carrying capacity of spacecraft, etc., to achieve The effects of eliminating extra propellant consumption, reducing disturbance torque, and improving utilization efficiency
- Summary
- Abstract
- Description
- Claims
- Application Information
AI Technical Summary
Problems solved by technology
Method used
Image
Examples
Embodiment Construction
[0030] Below in conjunction with accompanying drawing and specific embodiment the present invention is described in further detail:
[0031] The invention proposes an electric propulsion deployment and thrust direction adjustment mechanism, which improves the backup capability of the electric thruster and reduces the propellant consumption under faulty ignition conditions; the invention can also simultaneously improve the efficiency of the electric thruster for maintaining the north-south position
[0032] Such as figure 1Shown is a schematic structural diagram of the deployment and thrust direction adjustment mechanism. It can be seen from the figure that an electric propulsion deployment and thrust direction adjustment mechanism includes a mounting base plate 1, an elastic deployment joint 2, a first deployment arm 3, a locking mechanism 4, and a single degree of freedom Rotary joint 5, second deployment arm 6, double-degree-of-freedom rotary joint 7 and thruster mounting pl...
PUM
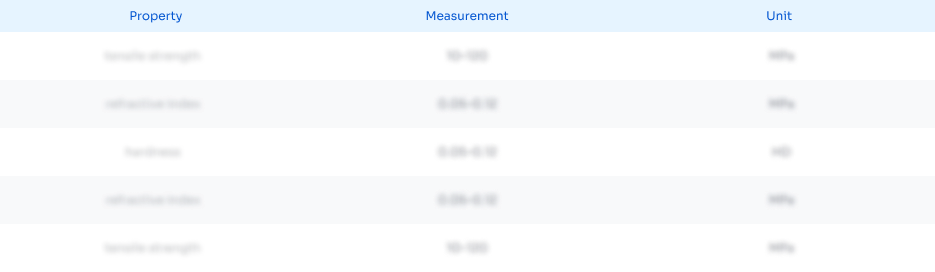
Abstract
Description
Claims
Application Information

- R&D
- Intellectual Property
- Life Sciences
- Materials
- Tech Scout
- Unparalleled Data Quality
- Higher Quality Content
- 60% Fewer Hallucinations
Browse by: Latest US Patents, China's latest patents, Technical Efficacy Thesaurus, Application Domain, Technology Topic, Popular Technical Reports.
© 2025 PatSnap. All rights reserved.Legal|Privacy policy|Modern Slavery Act Transparency Statement|Sitemap|About US| Contact US: help@patsnap.com