Total-reflection optical waveguide semiconductor laser chip and manufacturing method thereof
A laser and semiconductor technology, applied to the structure of optical waveguide semiconductors, etc., can solve problems affecting chip heat dissipation and increasing chip thermal resistance, and achieve the effects of eliminating stray light, improving reliability, and improving photoelectric conversion efficiency
- Summary
- Abstract
- Description
- Claims
- Application Information
AI Technical Summary
Problems solved by technology
Method used
Image
Examples
Embodiment 1
[0040] In this embodiment, taking a laser with a wavelength of 650 nm as an example, the preparation process of the semiconductor laser chip of the present invention is described in detail, which specifically includes the following steps.
[0041] (1) Utilize the metal organic chemical vapor deposition method to grow the lower cladding layer 3, the active region 4, the upper cladding layer 5 and the ohmic contact layer 6 sequentially on the substrate 2 to form an epitaxial wafer, such as figure 1 shown.
[0042] (2) One-time photolithography: evenly cover a layer of photoresist on the ohmic contact layer 6, and form a ridge-shaped optical cavity 9 with a certain width according to the design requirements along the direction perpendicular to the cleavage of the epitaxial wafer through exposure, development and corrosion. The laser bar with a certain period and a certain width of the isolation groove 10, the height of the ridge optical cavity 9 is less than the thickness of the ...
Embodiment 808
[0057] In this embodiment, an 808nm wavelength laser is taken as an example.
[0058] The difference between this embodiment and embodiment 1 is:
[0059] In step (2), through exposure, development, and etching, along the direction perpendicular to the cleavage of the epitaxial wafer, a laser stripe structure with an optical cavity width of 50 microns, a period of 200 microns, and an isolation groove width of 20-30 microns is formed.
[0060] In step (3), each layer of SiO 2 Dielectric film thickness = 808nm*1 / (4*1.54) = 131nm, each layer of TiO 2 Dielectric film thickness=808nm*1 / (4*2.70)=75nm.
PUM
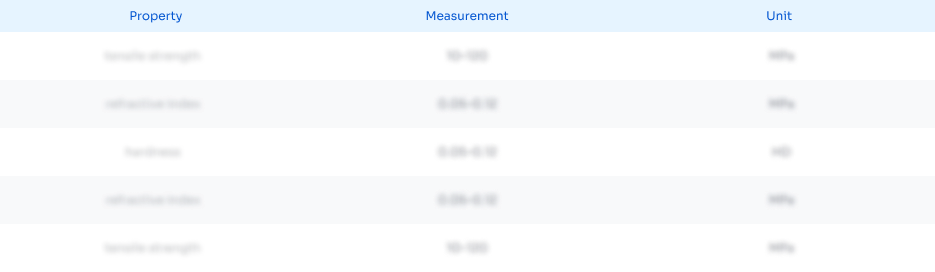
Abstract
Description
Claims
Application Information

- R&D Engineer
- R&D Manager
- IP Professional
- Industry Leading Data Capabilities
- Powerful AI technology
- Patent DNA Extraction
Browse by: Latest US Patents, China's latest patents, Technical Efficacy Thesaurus, Application Domain, Technology Topic, Popular Technical Reports.
© 2024 PatSnap. All rights reserved.Legal|Privacy policy|Modern Slavery Act Transparency Statement|Sitemap|About US| Contact US: help@patsnap.com