Three-arm star-shaped multi-block UV resin for matte coating and preparation method thereof
A multi-block, resin technology, applied in coatings, polyurea/polyurethane coatings, etc., can solve the problems of affecting coating effects, adverse effects on production, and difficulty in perfect mutual solubility, achieving shortened production cycles, short curing time, and high energy efficiency. The effect of less consumption
- Summary
- Abstract
- Description
- Claims
- Application Information
AI Technical Summary
Problems solved by technology
Method used
Image
Examples
Embodiment 1
[0045] Weigh 66.69g (0.3mol) of isophorone diisocyanate and place it in a reaction kettle, add 0.02g of catalyst dibutyltin dilaurate, heat to 50°C, and blow nitrogen. 34.83 g (0.3 mol) of hydroxyethyl acrylate was added, the addition time was 4 hours, and the reaction was kept for 5 hours.
[0046]Weigh 13.42g (0.1mol) of trimethylolpropane and place it in a reaction kettle, add 0.01g of catalyst dibutyltin dilaurate, heat to 60°C, and blow nitrogen. Weigh 66.69 g (0.3 mol) of isophorone diisocyanate and slowly add it into the reaction kettle, the feeding time is 5 hours, and the reaction is kept for 3 hours. Weigh 600 g (0.3 mol) of polyethylene glycol with a molecular weight of 2000 g / mol, slowly add it into the reaction kettle, the feeding time is 3 hours, and the reaction is kept for 4 hours. Add 0.005g of catalyst dibutyltin dilaurate, and slowly add 101.52g (0.3mol) of isocyanate-terminated acrylate dimer into the reaction kettle for 4 hours of feeding time and 5 hours...
Embodiment 2
[0049] Weigh 66.69g (0.3mol) of isophorone diisocyanate and place it in a reaction kettle, add 0.02g of catalyst dibutyltin dilaurate, heat to 50°C, and blow nitrogen. 39.04 g (0.3 mol) of hydroxyethyl methacrylate was added, the addition time was 4 hours, and the reaction was kept for 5 hours.
[0050] Weigh 13.42g (0.1mol) of trimethylolpropane and place it in a reaction kettle, add 0.01g of catalyst dibutyltin dilaurate, heat to 60°C, and blow nitrogen. Weigh 66.69 g (0.3 mol) of isophorone diisocyanate and slowly add it into the reaction kettle, the feeding time is 5 hours, and the reaction is kept for 3 hours. Weigh 300 g (0.3 mol) of polyethylene glycol with a molecular weight of 1000 g / mol, slowly add it into the reaction kettle, the feeding time is 3 hours, and the reaction is kept for 4 hours. Add 0.005g of catalyst dibutyltin dilaurate, and slowly add 105.73g (0.3mol) of isocyanate-terminated acrylate dimer into the reaction kettle. The feeding time is 4 hours, and ...
Embodiment 3
[0053] Weigh 66.69g (0.3mol) of isophorone diisocyanate and place it in a reaction kettle, add 0.02g of catalyst dibutyltin dilaurate, heat to 50°C, and blow nitrogen. 43.25 g (0.3 mol) of hydroxypropyl methacrylate was added, the addition time was 4 hours, and the reaction was kept for 5 hours.
[0054] Weigh 13.42g (0.1mol) of trimethylolpropane and place it in a reaction kettle, add 0.01g of catalyst dibutyltin dilaurate, heat to 60°C, and blow nitrogen. Weigh 66.69 g (0.3 mol) of isophorone diisocyanate and slowly add it into the reaction kettle, the feeding time is 5 hours, and the reaction is kept for 3 hours. Weigh 900 g (0.3 mol) of polyethylene glycol with a molecular weight of 3000 g / mol, slowly add it into the reaction kettle, the feeding time is 3 hours, and the reaction is kept for 4 hours. Add 0.005g of catalyst dibutyltin dilaurate, and slowly add 109.94g (0.3mol) of isocyanate-terminated acrylate dimer into the reaction kettle. The feeding time is 4 hours, and...
PUM
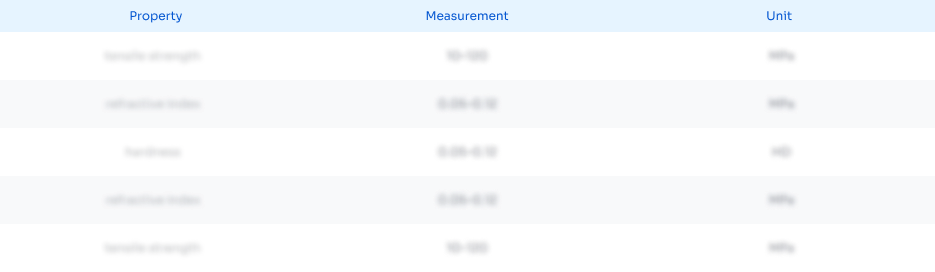
Abstract
Description
Claims
Application Information

- R&D Engineer
- R&D Manager
- IP Professional
- Industry Leading Data Capabilities
- Powerful AI technology
- Patent DNA Extraction
Browse by: Latest US Patents, China's latest patents, Technical Efficacy Thesaurus, Application Domain, Technology Topic, Popular Technical Reports.
© 2024 PatSnap. All rights reserved.Legal|Privacy policy|Modern Slavery Act Transparency Statement|Sitemap|About US| Contact US: help@patsnap.com