Method for improving quality of Al-Cu dissimilar metal friction stir welding butt joint
A technology of friction stir welding and dissimilar metals, which is applied in the direction of welding/welding/cutting articles, welding equipment, metal processing equipment, etc., and can solve the problem of not significantly improving the welding quality of friction stir welding joints of Al-Cu dissimilar metals, joint machinery There is no obvious improvement in performance, etc., to achieve the effect of improving mechanical properties, simple machining, and simple processing methods
- Summary
- Abstract
- Description
- Claims
- Application Information
AI Technical Summary
Problems solved by technology
Method used
Image
Examples
Embodiment 1
[0023] 1) Processing of weldments with serrated edges: Take a piece of 6061-T6 aluminum alloy and T2 copper plate with a length of 100mm, a width of 50mm, and a thickness of 4mm, and process the two plates along the welding butt joint edge to produce trapezoidal sawtooth, and the length of the long side of the trapezoid is is 3.00mm, the length of the short side is 1.27mm, the height is 1.5mm, and the interval between each sawtooth is 1.5mm.
[0024] Use sandpaper to remove the oxide skin on the surface of the welding and serrated edges, and then wipe with alcohol to remove the oil stains and other impurities on the weldment.
[0025] 2) Friction stir welding: Firstly, the two weldments processed above are butted together along the sawtooth edge. Misalignment and offset are not allowed in the butt joint, and the maximum butt gap is less than 0.2mm. Then the butt-connected test plate was fixed horizontally on the welding platform of the friction stir welding machine for welding...
Embodiment 2
[0028] 1) Processing of weldments with serrated edges: Take a piece of 7075 aluminum alloy and a brass plate with a length of 100mm, a width of 50mm, and a thickness of 5mm, and process the two plates along the butt edge to form a trapezoidal sawtooth. The long side of the trapezoid is 3.00mm, The short side is 1.27mm, the height is 1.5mm, and the interval between each sawtooth is 1.5mm.
[0029] Use sandpaper to remove the oxide skin on the welding surface, and then wipe with alcohol to remove oil and other impurities on the test plate.
[0030] 2) Friction stir welding: butt the processed two test plates along the sawtooth edge, the butt joint sawtooth is not allowed to have misalignment and offset, and the maximum butt joint gap does not exceed 0.25mm. Then the butted test plate is fixed horizontally on the welding platform of the friction stir welding machine for welding.
[0031] The specific process parameters of welding are: the spindle speed is 800rpm, the stirring to...
Embodiment 3
[0033] 1) Processing of weldments with serrated edges: take industrial pure aluminum and T2 copper pipe fittings of φ500, length 250mm, and thickness 3mm, and process trapezoidal serrations evenly along the butt rings of these two pipe fittings. The long side of the trapezoidal serrations is 3.00mm, The short side is 1.27mm and the height is 1.5mm.
[0034] Use sandpaper to remove the oxide skin on the welding surface, and then wipe with alcohol to remove oil and other impurities on the test plate.
[0035] 2) Friction stir welding: butt the above-mentioned two pipe fittings along the sawtooth edge, the butt joint serrations are not allowed to have misalignment and offset, and the maximum butt joint gap is less than 0.15mm. Then the butt welded parts are clamped on the friction stir welding machine welding of the girth weld for welding.
[0036] The specific process parameters of welding are: the spindle speed is 600rpm, and the stirring tool travel speed is 50mm / min. The st...
PUM
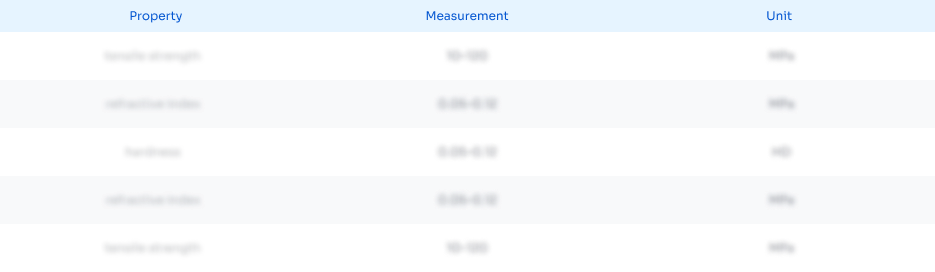
Abstract
Description
Claims
Application Information

- R&D Engineer
- R&D Manager
- IP Professional
- Industry Leading Data Capabilities
- Powerful AI technology
- Patent DNA Extraction
Browse by: Latest US Patents, China's latest patents, Technical Efficacy Thesaurus, Application Domain, Technology Topic, Popular Technical Reports.
© 2024 PatSnap. All rights reserved.Legal|Privacy policy|Modern Slavery Act Transparency Statement|Sitemap|About US| Contact US: help@patsnap.com