Preparation method of amphoteric polycarboxylate-type slump loss resistance agent
An amphoteric polycarboxylic acid and slump-retaining agent technology, applied in the field of concrete functional admixtures, can solve the problem of insufficient slump retention time, too fast release of slump retention performance, and difficulty in meeting the requirements of long-term, long-distance transportation and construction of fresh concrete. problems, to achieve the effect of improving work adaptability
- Summary
- Abstract
- Description
- Claims
- Application Information
AI Technical Summary
Problems solved by technology
Method used
Image
Examples
Embodiment 1
[0021] In a 1L glass flask, add 300g deionized water, 350g methallyl polyoxyethylene ether (molecular weight 2400), 1.8g hydrogen peroxide (27.5%), and mix well. Turn on the stirring and raise the temperature to 60°C. Begin to drop mixed solution A (composed of: 10g acrylic acid+20g hydroxyethyl acrylate+50g 2-methacryloyloxyethyl phosphorylcholine+100g deionized water) and mixed solution B (made up of: Vc 0.9g + 1.5g 2-mercaptopropionic acid+ 160g deionized water), evenly added dropwise within 3 hours. After holding at 60°C for 1 hour, the solution was cooled to 40-50°C. Add appropriate amount of deionized water and 32% NaOH, adjust the system to about pH 6.0, and prepare the amphoteric polycarboxylate superplasticizer aSP-1 with a solid content of 40%.
Embodiment 2
[0023] In a 1L glass flask, add 150g deionized water, 320g allyl polyoxyethylene ether (molecular weight 1200), 50g maleic anhydride, and mix well. Turn on the stirring and raise the temperature to 75°C. Start to drop mixed solution A (composed of: 6g hydroxyethyl acrylate + 25g 2-methacryloyloxyethyl phosphorylcholine + 4g sodium methallylsulfonate + 200g deionized water) and mixed solution B respectively (Composition: 10g sodium persulfate+180g deionized water), the uniform dropwise addition was completed within 2 hours. After holding at 75°C for 1 hour, the temperature of the solution was lowered to 40-50°C. Add appropriate amount of deionized water and 32% NaOH, adjust the system to about pH 6.0, and prepare the amphoteric polycarboxylate superplasticizer aSP-2 with a solid content of 40%.
Embodiment 3
[0025] In a 1L glass flask, add 250g of deionized water, 360g of prenyl polyoxyethylene ether (molecular weight 3000), 1.0g of hydrogen peroxide (27.5%), and mix well. Turn on the stirring and raise the temperature to 25-30°C. Begin to drop mixed solution A (composed of: 8g acrylic acid+25g hydroxypropyl acrylate+65g 2-methacryloyloxyethyl phosphorylcholine+100g deionized water) and mixed solution B (made up of: Vc 0.5g + 2.3g mercaptoacetic acid + 100g deionized water), the uniform dropwise addition was completed within 2 hours, and the system automatically heated up to 40-45°C during the polymerization process. After holding at 40-45°C for 2 hours, add an appropriate amount of deionized water and 32% NaOH to adjust the system to about pH 6.0 to prepare an amphoteric polycarboxylate-type water reducer aSP-3 with a solid content of 40%.
PUM
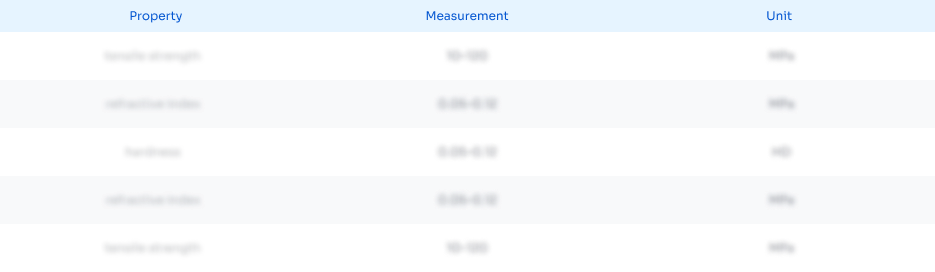
Abstract
Description
Claims
Application Information

- R&D
- Intellectual Property
- Life Sciences
- Materials
- Tech Scout
- Unparalleled Data Quality
- Higher Quality Content
- 60% Fewer Hallucinations
Browse by: Latest US Patents, China's latest patents, Technical Efficacy Thesaurus, Application Domain, Technology Topic, Popular Technical Reports.
© 2025 PatSnap. All rights reserved.Legal|Privacy policy|Modern Slavery Act Transparency Statement|Sitemap|About US| Contact US: help@patsnap.com