Anti-alkali metal poisoning denitrification catalyst and preparation method thereof
A denitration catalyst, alkali metal technology, applied in catalyst activation/preparation, molecular sieve catalysts, chemical instruments and methods, etc., can solve the problems of insignificant benefits, can not fully meet the needs of anti-alkali metal poisoning, etc., achieve good selectivity, The effect of strong resistance to alkali metal poisoning and wide temperature window
- Summary
- Abstract
- Description
- Claims
- Application Information
AI Technical Summary
Problems solved by technology
Method used
Examples
Embodiment 1
[0029] The H-SAPO-34 molecular sieve was prepared by hydrothermal method. Dissolve 17.3468g of ammonium chloride in 100ml of deionized water, add 5g of H-SAPO-34 into it, adjust the pH value to 3.5 with hydrochloric acid, stir at 80°C for 2h, filter, and dry in an oven at 120°C overnight to obtain NH 4 -SAPO-34. Dissolve 0.6242g of copper sulfate in 100ml of deionized water, add 1g of NH 4 Add -SAPO-34 into it, ion exchange at 80°C for 3h, filter, wash, dry overnight at 120°C, and calcined at 550°C for 5h to obtain Cu-SAPO-34 molecular sieve. Then 0.2073g of potassium carbonate, 0.9584g of titanium dioxide, and 0.3157g of manganese trioxide were mixed uniformly and fully ground, and placed in a muffle furnace for calcination in air at 1000°C for 8h. Treat the obtained powder with a mixed acid of sulfuric acid and nitric acid (volume ratio 3:1) at 80°C for 3 hours, filter and wash until neutral. Then mix the Cu-SAPO-34 obtained above with the spessartite oxide after acid tre...
Embodiment 2
[0032] The H-SAPO-34 molecular sieve was prepared by hydrothermal method. Dissolve 25.9581g of ammonium nitrate in 100ml of deionized water, add 5g of H-SAPO-34 into it, adjust the pH value to 3.5 with nitric acid, stir at 80°C for 2h, filter, and dry in an oven at 120°C overnight to obtain NH 4 -SAPO-34. Dissolve 0.6242g of copper sulfate in 100ml of deionized water, add 1g of NH 4 -SAPO-34 was added to it for ion exchange at 80°C for 3h, filtered, washed, dried overnight at 120°C, and calcined at 550°C for 5h to obtain Cu-SAPO-34 molecular sieve. Then 0.2073g of potassium carbonate, 0.9584g of titanium dioxide, and 0.3157g of manganese trioxide were mixed uniformly and fully ground, and placed in a muffle furnace for calcination in air at 1000°C for 8h. Treat the obtained powder with a mixed acid of sulfuric acid and nitric acid (volume ratio 3:1) at 80°C for 3 hours, process twice, filter and wash until neutral. Then, the Cu-SAPO-34 obtained above and the spessartite oxi...
Embodiment 3
[0035] The H-SAPO-34 molecular sieve was prepared by hydrothermal method. Dissolve 17.3468g of ammonium chloride in 100ml of deionized water, add 5g of H-SAPO-34 into it, adjust the pH value to 3.5 with hydrochloric acid, stir at 80°C for 2h, filter, and dry in an oven at 120°C overnight to obtain NH 4 -SAPO-34. Dissolve 0.4689g of copper nitrate in 100ml of deionized water, 1g of NH 4 Add -SAPO-34 into it, ion exchange at 80°C for 4h, filter, wash, dry overnight at 120°C, and calcined at 550°C for 5h to obtain Cu-SAPO-34 molecular sieve. Then 0.2073g of potassium carbonate, 0.9584g of titanium dioxide, and 0.3157g of manganese trioxide were mixed uniformly and fully ground, and placed in a muffle furnace for calcination in air at 1000°C for 8h. Treat the obtained powder with a mixed acid of sulfuric acid and nitric acid (volume ratio 3:1) at 80°C for 3 hours, process twice, filter and wash until neutral. Then mix the Cu-SAPO-34 obtained above with the spessartite oxide aft...
PUM
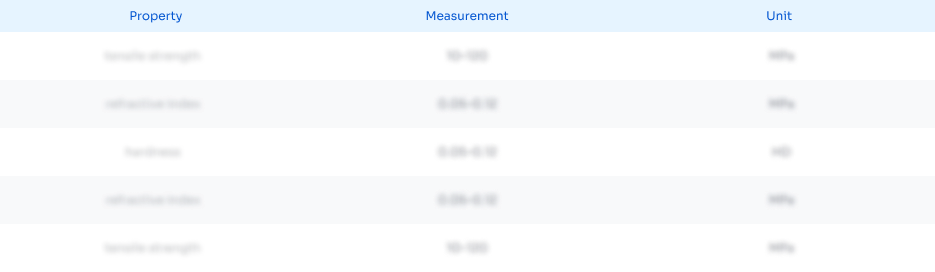
Abstract
Description
Claims
Application Information

- R&D Engineer
- R&D Manager
- IP Professional
- Industry Leading Data Capabilities
- Powerful AI technology
- Patent DNA Extraction
Browse by: Latest US Patents, China's latest patents, Technical Efficacy Thesaurus, Application Domain, Technology Topic, Popular Technical Reports.
© 2024 PatSnap. All rights reserved.Legal|Privacy policy|Modern Slavery Act Transparency Statement|Sitemap|About US| Contact US: help@patsnap.com