Method for preparing lanthanum oxide through microwave calcination
A lanthanum oxide, calcining technology, applied in chemical instruments and methods, rare earth metal oxides/hydroxides, inorganic chemistry, etc., can solve the problems of limited kiln body life, long roasting time, large equipment investment, etc., and achieve easy realization. The effect of industrialized production, overcoming long production cycle and improving product quality
- Summary
- Abstract
- Description
- Claims
- Application Information
AI Technical Summary
Problems solved by technology
Method used
Examples
Embodiment 1
[0019] This example provides a method for preparing lanthanum oxide by microwave calcination. This method avoids the disadvantages of over-burning and under-burning of materials caused by the easy formation of temperature gradients in traditional calcination methods, and has the advantages of short calcination time, low energy consumption, uniform heating, and high product quality. Stable, easy to achieve automatic control and other advantages. details as follows:
[0020] Put the lanthanum salt in a ceramic crucible, put it in a microwave experimental furnace, turn on the microwave, raise the temperature to 1250°C in stages for calcination, keep the heating rate at a constant speed, and keep it warm every time it rises to a temperature step. After the calcination, the crucible was taken out and cooled to room temperature naturally to obtain the lanthanum oxide product. After testing and analysis, the chemical composition and particle size of lanthanum oxide products have rea...
Embodiment 2
[0022] This example provides a method for preparing lanthanum oxide by microwave calcination. This method avoids the disadvantages of over-burning and under-burning of materials caused by the easy formation of temperature gradients in traditional calcination methods, and has the advantages of short calcination time, low energy consumption, uniform heating, and high product quality. Stable, easy to achieve automatic control and other advantages. details as follows:
[0023] Take 100g of lanthanum carbonate powder with a particle size of less than 100 mesh and a moisture content of 3.5wt%, and put it in a ceramic crucible, and place it in a microwave experimental furnace. Start the microwave segmental heating and calcination program, control the microwave output power to 500W, and the frequency to 2.45GHz , the heating rate is controlled at 10°C / min, the temperature is raised to 350°C in the first stage, and kept for 60 minutes; the temperature is raised to 850°C in the second s...
Embodiment 3
[0025] This example provides a method for preparing lanthanum oxide by microwave calcination. This method avoids the disadvantages of over-burning and under-burning of materials caused by the easy formation of temperature gradients in traditional calcination methods, and has the advantages of short calcination time, low energy consumption, uniform heating, and high product quality. Stable, easy to achieve automatic control and other advantages. details as follows:
[0026] Take 100g of lanthanum carbonate powder with a particle size of less than 100 mesh and a moisture content of 3.5wt% in a ceramic crucible, and place it in a microwave experimental furnace, start the microwave segmental heating and calcination program, control the microwave output power to 1500W, and the frequency to 2.45GHz , the heating rate is controlled at 15°C / min, the temperature is raised to 200°C in the first stage, and kept for 30 minutes; the temperature is raised to 700°C in the second stage, and k...
PUM
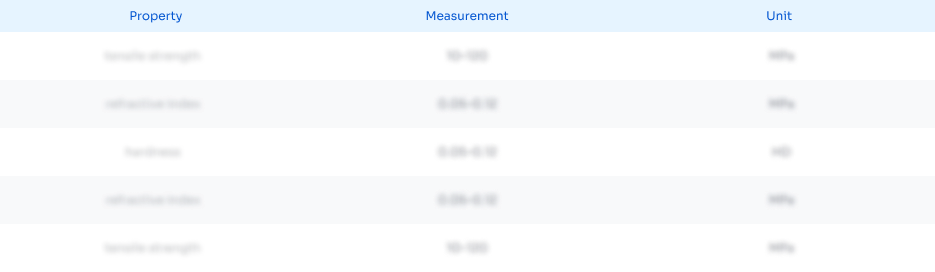
Abstract
Description
Claims
Application Information

- Generate Ideas
- Intellectual Property
- Life Sciences
- Materials
- Tech Scout
- Unparalleled Data Quality
- Higher Quality Content
- 60% Fewer Hallucinations
Browse by: Latest US Patents, China's latest patents, Technical Efficacy Thesaurus, Application Domain, Technology Topic, Popular Technical Reports.
© 2025 PatSnap. All rights reserved.Legal|Privacy policy|Modern Slavery Act Transparency Statement|Sitemap|About US| Contact US: help@patsnap.com